Chain Gang
Whiting & Davis’s flat, brass mesh makes a unique curtain or wall covering.
It’s not often that a company is saved by its employees. But when Sperian, the French conglomerate that owned Whiting & Davis, decided to shut down the historical Attleboro Falls mesh manufacturing facility in 2010, plant manager Darrin Cutler saw an opportunity. Cutler relished the 136-year-old company’s history and believed he could expand the market for its exquisite specialty products.
Founded by two silversmiths, Whiting & Davis is one of the oldest continuously operating jewelry factories in the country. The company started making its signature metal mesh more than 120 years ago. At that time, the process was arduous. Individual metal rings or flat circles were attached to one another by hand with the aid of a four-pronged clamp. Made of silver and gold, the resulting mesh was fashioned in one of two forms: flat or ring (also called chain mail). Fabric-like and eye-catching, the material was then incorporated into jewelry and purses.
In the early 1900s, Whiting & Davis teamed up with an inventor to create the world’s first automated mesh machine, which mechanically folded, clamped, and welded the rings into narrow sheets. With this new tool, the company could mass-produce its signature bags, now considered prize vintage finds. Demand soared and the company ballooned to 800 employees with eight international sales offices. And after a 1923 Broadway show featured their metal fabric as a backdrop, it was suddenly a must-have décor element.
Over the decades, the company’s focus shifted from fashion to personal safety (protective cutting gloves, butcher’s aprons, shark suits for scuba divers). By the mid-2000s, sales manager Lélia Teixeira was working with a tiny marketing budget to advertise their décor and fashion lines, but the orders continued to come in.
When Sperian decided to divest itself of the American facility, Cutler bought it, and he and Teixeira teamed up to revive the stylish side of Whiting & Davis’s business. Their diverse portfolio ranges from delicate jewelry in precious metals to industrial-strength gloves to sparkling metal curtains and room dividers, much of it commissioned by high-end fashion houses and big designers.
Since taking over, Cutler has come to expect the unexpected. “You never know who is going to be on the other end of that call,” he says of the wide-ranging demand for W & D products. “We’ve done projects for everyone from Donna Karan to John Deere.”
Regardless of where it will end up, making mesh is still demanding — the machines are only marginally different from those first developed in the early 20th century. Not far from the Rhode Island border, on the factory’s assembly line, machines clack and whir as engineering technicians hop from one station to the next adjusting the newly formed reams of mesh.
While perhaps tedious, mesh-making “was once a celebrated profession,” Cutler says. “They all wore bow ties to work and took great pride in it.” To this day, each technician receives nearly a year’s worth of training to operate Whiting & Davis’s 35 machines.
Once fabricated, the reams go through a quick degreasing wash before arriving in an assembly room, where a few women painstakingly craft the sheets into a wide range of products. On one recent day, they are making a 13-inch-wide panel to be used for an architectural drape; 2-by-2-foot squares for a collection of luxury-brand toss pillows; and a smaller custom-order panel with tiny divots that a prominent jewelry company will fill with crystals before turning it into a microphone cover.
“People wonder why it’s a costly material, and this is why,” Teixeira says, gesturing to a woman laboring over a piece of mesh. She is using a tool that resembles a knitting needle to join two panels together.
Most of Whiting & Davis’s décor orders come from architects, interior designers, and the occasional design-savvy homeowner, but Cutler has plans to offer standard-size mesh curtains directly to customers through W & D’s website. This spring, they also opened a showroom and design studio behind the factory. In the new space, designers can peruse the available options or work with the team to dream up their own. “Room dividers, curtains, lampshades, napkin rings, table runners … the possibilities are limitless,” says Cutler.
Rows of machines produce brass, stainless steel, and gold mesh.
These spools of attachment rings are fed into machines to manufacture flat mesh.
Hand stitching is required to create chain mail.
Simple hand tools and perfect eyesight are needed to repair black-and gold-finished brass mesh before its final use.
Technicians painstakingly examine each ring for flaws.
Whiting & Davis produces 18-karat gold and sterling silver fabrics for high-end jewelry lines.
A luxury-brand throw pillow made from stitched-together panels.
Whiting & Davis updates some of its original molds for contemporary designs.
Bins of mesh will be used to make architectural drapes, decorative pillows, and other custom luxury products.
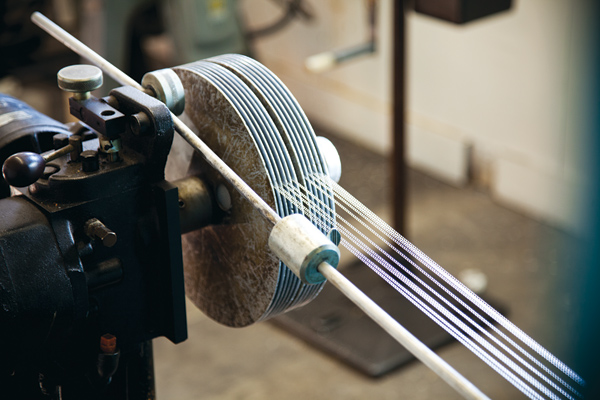
Photograph by Pat Piasecki
Strands of attachment rings are fed into the mesh-making machine to create narrow panels of fabric.
Panels can be measured and cut down to size.
Depending on the size of the mesh, technicians use an arsenal of hand tools to join the panels into a final design.