Dyed in Wool
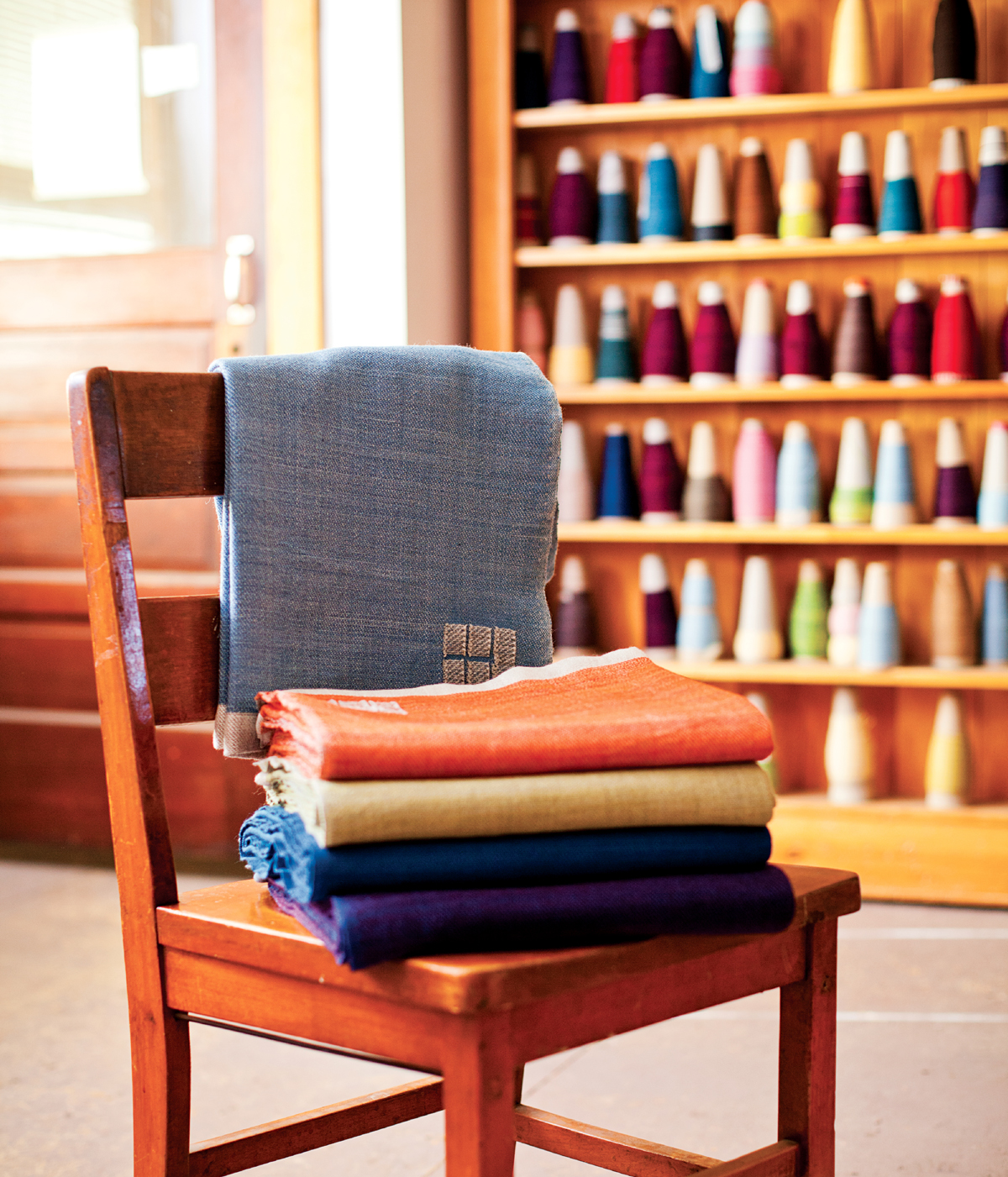
Swans Island Company’s naturally dyed “Katahdin” throws await shipment in front of a wall of yarn. (Photograph by Pat Piasecki)
Back in the early ’90s, Boston lawyers John and Carolyn Grace fled their downtown law practices for the serenity of Swan’s Island, an 80-square-mile lobstering community off the coast of Maine, near Bar Harbor. They’d summered there for years, and were looking for a full-time reprieve from the daily grind—one that would allow them to live and work closely with the land. Like hundreds of other islands off the rocky coast, Swan’s Island had traditionally been used to raise sheep for Maine’s many textile mills, and the couple took advantage of this rich history by starting a small blanket-weaving operation. They went as far as to make their own natural dyes and master massive wooden hand looms.
When Bill Laurita bought the Swans Island Blanket Company more than a decade later, he moved it from its original home to a new location in the coastal town of Northport. There, the former Waldorf school teacher apprenticed with the Graces and experimented with natural dyes on the porch of the company’s 1780s post-and-beam farmhouse before setting up a separate on-site dye house. Laurita, like the Graces, was dedicated to preserving not just the art of hand-weaving, but also to creating a sustainable, organic, U.S.-made product.
Under Laurita, the mill continues to produce the vibrant blankets, scarves, and throws that have won a Smithsonian Blue Ribbon and garnered attention from the likes of Martha Stewart and Michelle Obama.
Wool for winter blankets is sourced locally from Betty Hauger’s farm in Winterport, while lightweight summer blankets require wool from Corriedale sheep, which comes from as far away as Ohio. Once collected, the fleeces are sent to Green Mountain Spinnery, a worker-owned cooperative in Putney, Vermont, where they are whirled into lofty yarn. Then it’s off to the aforementioned dye house, where workers mix vats of vibrant hues with pigments found in nature: They get blues from the indigo plant and pinks from the shell of a cochineal beetle, similar to the ladybug.
Inside the attached weaving studio, artists like Cape Cod native Janet Moller operate hand looms as big as 5 feet across, using a foot pedal to raise and lower a harness attached to the warp thread. When the harness is up, a shuttle carries the weft thread (wrapped around the bobbin) across the loom in an under-one-over-two pattern called a twill weave. It takes Moller 9 to 10 hours to weave a winter blanket. “It’s actually quite meditative, because you get into a rhythm and are moving right along,” she says, noting that most of the weavers wear earplugs because the equipment is so loud.
Once a blanket has been woven, it’s sent to finishing, where artisans use tweezers to painstakingly remove the little bits of straw and hay that inevitably get caught in the sheep’s coat. “Some of our sheep wear little jackets to keep that chaff down, but it still gets in,” Laurita says. Since their wool is spun without any chemical treatment, it’s not just the chaff that’s left behind, but also the protective lanolin. “It makes the yarn last forever and gives it this beautiful, supple feel,” Laurita says.
Beauty and practicality are ingrained in Laurita like the warp and weft threads of a Swans Island Blanket. “Everything in my house has a story behind it and a practical application,” he says, citing a corkscrew collection eight years in the making. “Every time I use one I remember that trip to the outskirts of Paris and the flea market with all the stalls,” he says. “It’s the same with our blankets. Each one is truly an heirloom.”

Photographs by Pat Piasecki
Clockwise from top left, local wool is sent to Green Mountain Spinnery, in Putney, Vermont, where it’s spun into yarn; before making its way to the dye pot, the yarn gets wound through the skeining machine; skeins of yarn are colored naturally with house-made dyes; a linen/organic-cotton yarn in development.
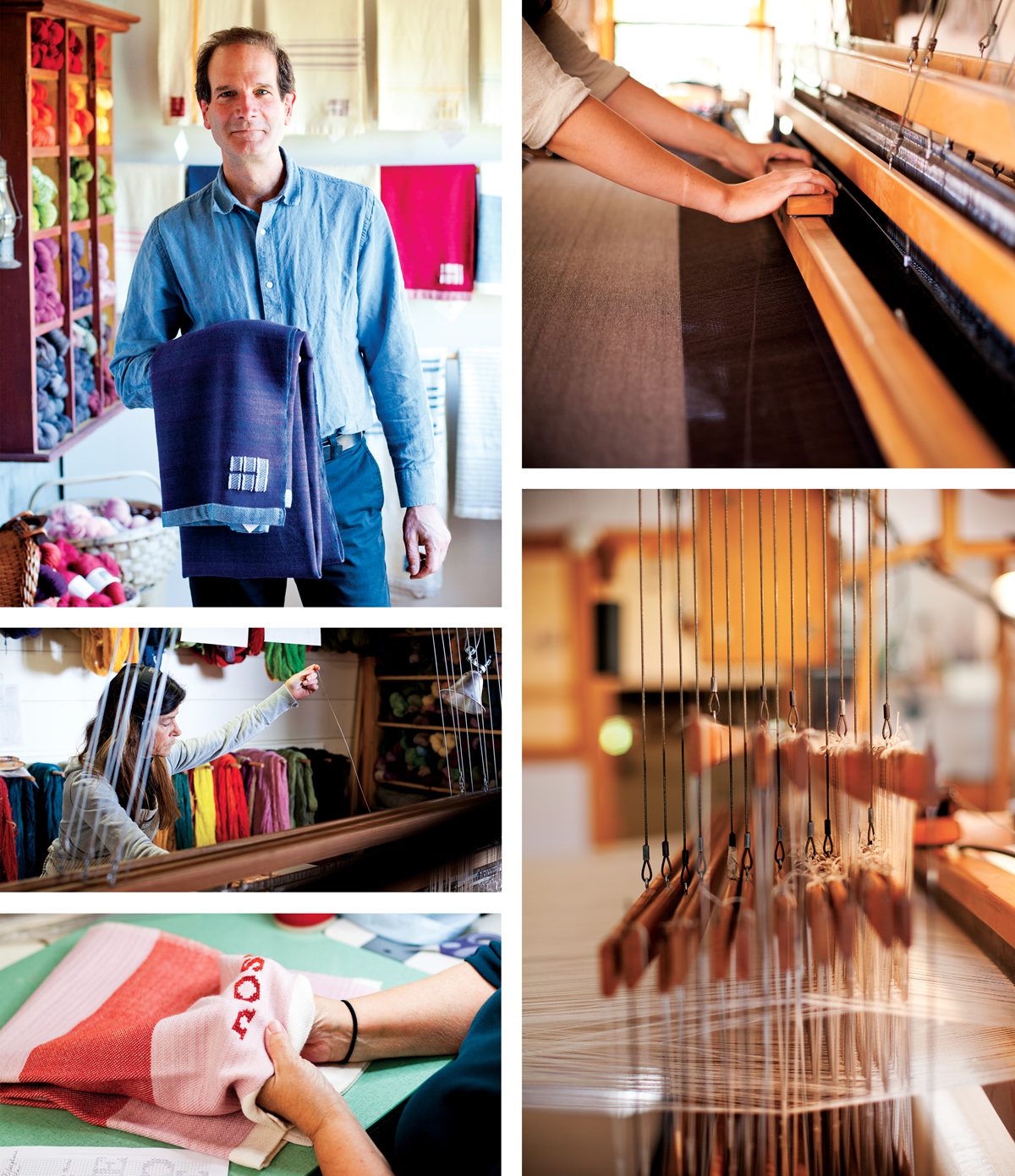
Photographs by Pat Piasecki
Clockwise from top left, Swans Island Company owner Bill Laurita poses with a merino throw; air-assisted hand looms were purchased from AVL, in California; warp (vertical) and weft (horizontal) threads pass through harnesses, on their way to becoming a blanket; a seamstress embroiders a baby blanket; a weaver adjusts a weft thread while working the loom.
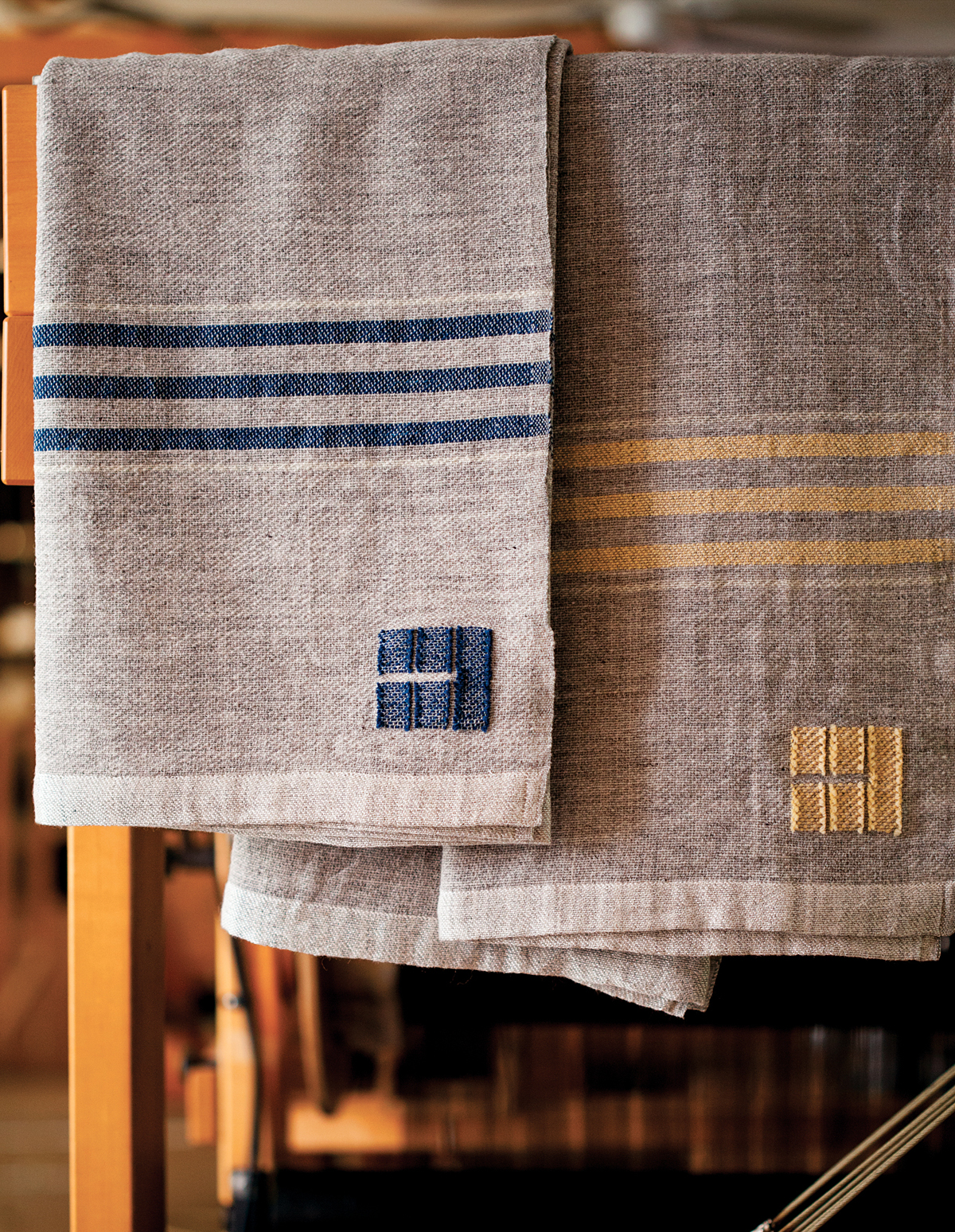
Photograph by Pat Piasecki
Above, lightweight summer throws are woven with fleece from Corriedale sheep.
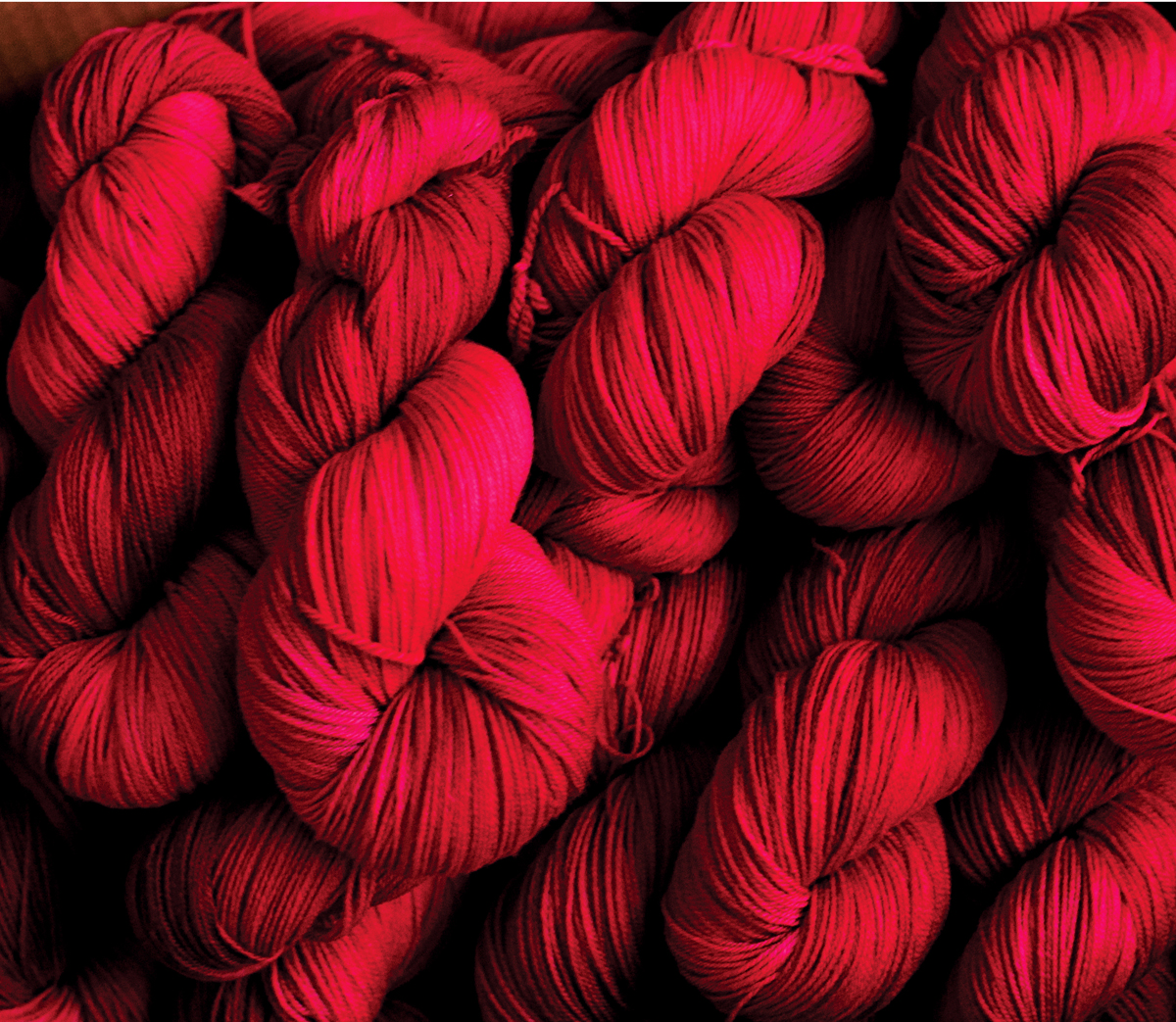
Photograph by Pat Piasecki
Employees at Swans Island Company use cochineal beetle shells to create vibrant red yarn.