New England Made: Nantucket Looms
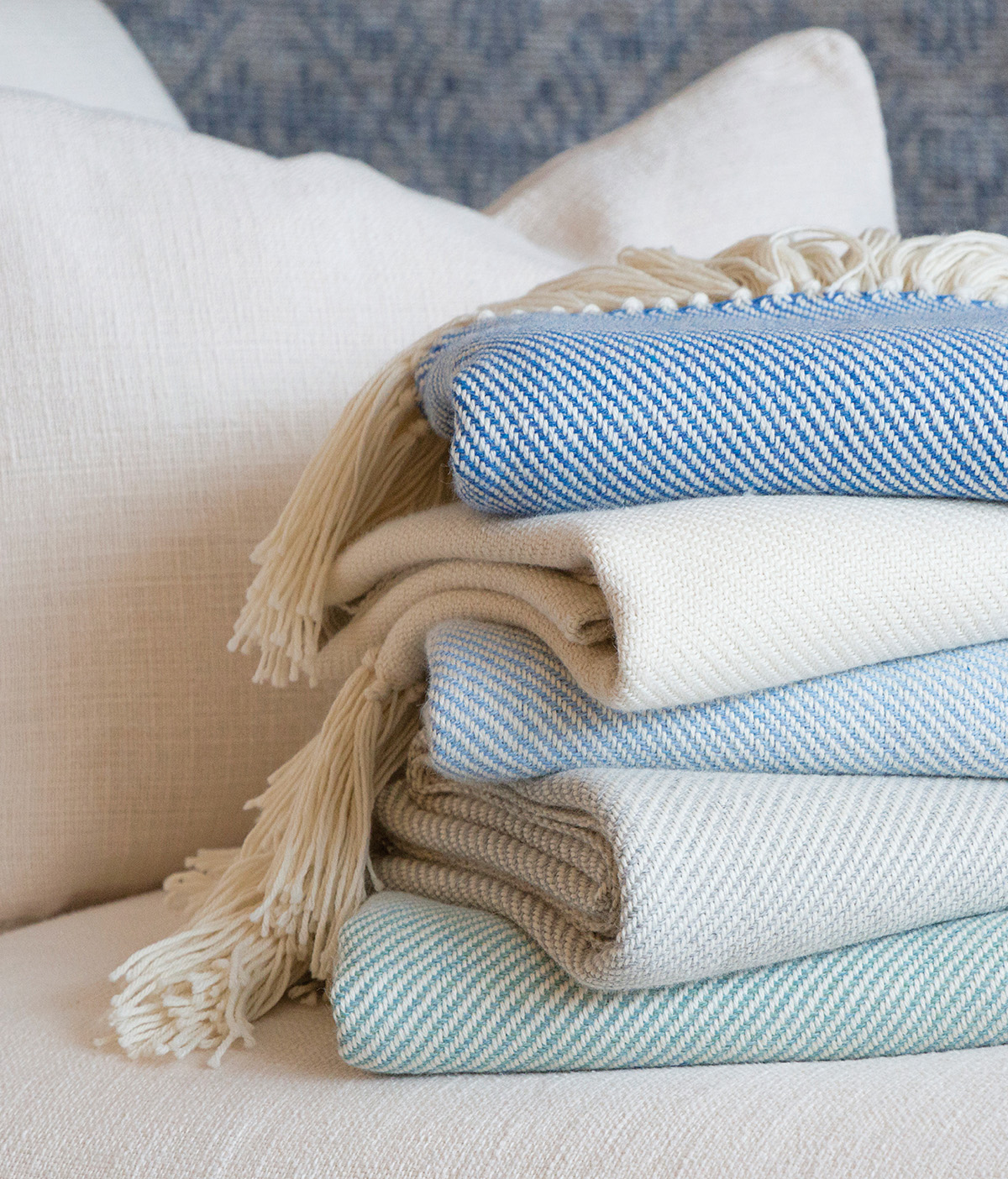
Courtesy Photo
Along the weathered cobblestones of Nantucket’s Main Street lies a small brick shop shaded by tall trees. On the second floor, several weavers patiently thread the heddles of their Maine-made Macomber wooden looms, some of which are older than the craftspeople themselves. The floorboards of the studio creak to their rhythmic work, as shuttles skate across the wefts like salt on the wind. Nantucket Looms has run its tiny manufacturing operation since 1968, while the neighborhood around it has transformed from fishermen’s shacks to high-end real estate.
Nantucket Looms’ founders, Bill Euler and Andy Oates, met while working at the Woodbox Inn in the late ’50s. Euler was a businessman, and Oates had trained as a weaver at Black Mountain College under iconic textile artist Anni Albers. Together, Euler and Oates adopted the “cottage style” aesthetic: a mix of folksy antiques and contemporary furnishings, with a focus on comfort. When the Nantucket Historical Trust in 1961 opened the Cloth Company, where needlepoint, crewelwork, weaving instruction, and handwoven fabrics were offered, Oates and Euler were installed to run it.
On April 1, 1968, the pair took ownership of the company, reopening it as Nantucket Looms. At the same time, interest in the island’s crafts movement swelled, and Euler and Oates nourished the local community by selling local works out of the ground-floor retail space; today, Nantucket Looms features pottery, soaps, candles, and clothing from more than 70 local artists.
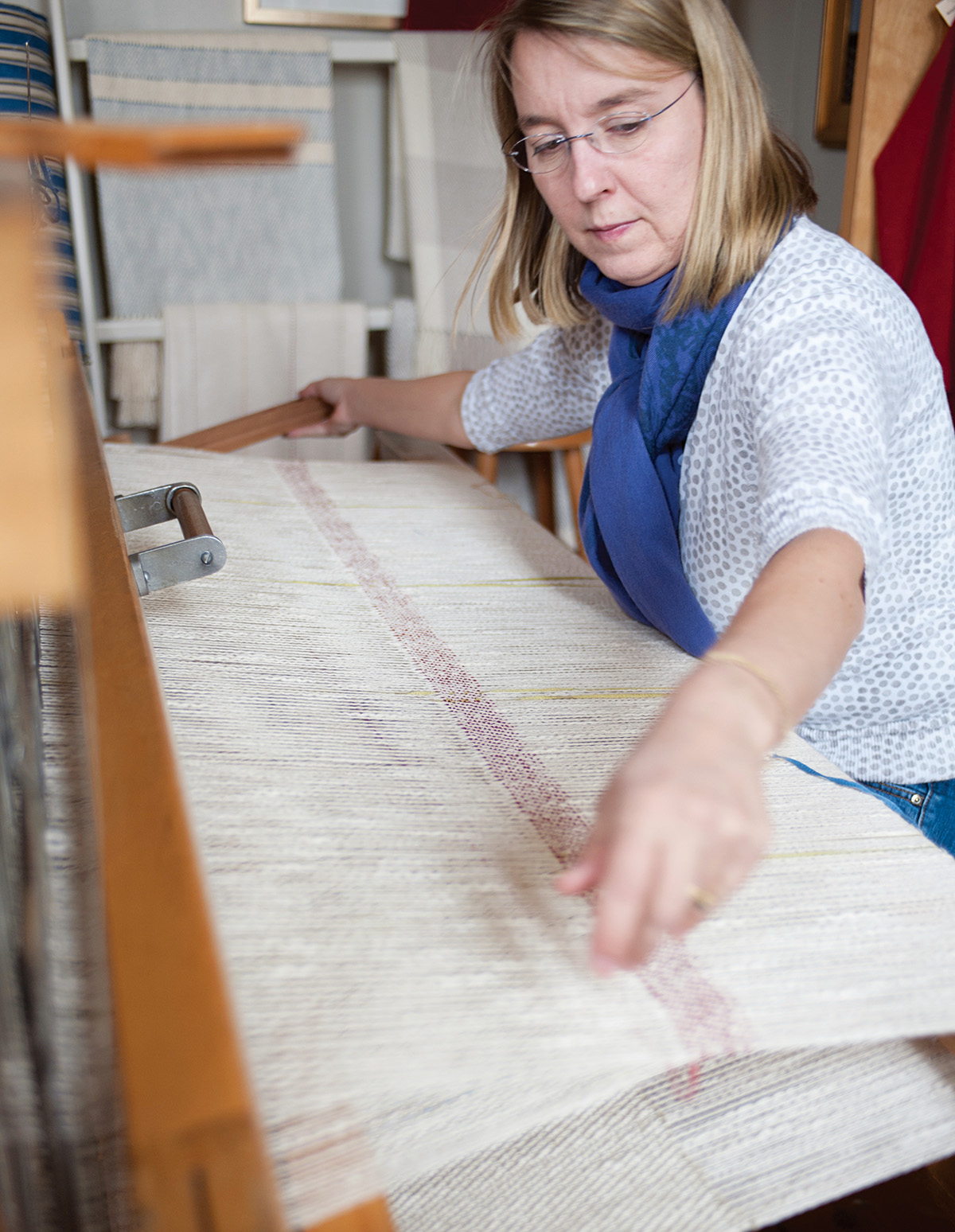
As she works on a throw, Rebecca Peraner guides the shuttle of her loom. / Courtesy Photo
To encourage a new generation of weavers, Oates and Euler welcomed apprentices, one of whom was Rhode Island School of Design student Rebecca Peraner. She had vacationed on Nantucket each summer with her family, and knew she wanted to live there someday; in college, she drew inspiration from the island’s landscapes, architecture, and colors to create patterns of her own. Like Oates, she thought of weaving as an art form, not simply a production method, and she returned to the company after graduating in 1995.
Oates and Euler retired in 1993, and Peraner took over as creative director and head weaver of Nantucket Looms in 2001. Peraner continues to take on apprentices and seasoned weavers who share her passion for the details that distinguish handwoven textiles from machine-made goods.
Each weaver works on eight to 16 items at a time, from throws and scarves to wraps and rugs. No two pieces are perfectly alike; weaving by hand allows Peraner and her team to make each creation personal. “It’s extremely rewarding when someone comes into the studio and actually understands that it wasn’t made by a machine,” Peraner says. “Textiles are all-encompassing. The textures are part of our daily lives.”
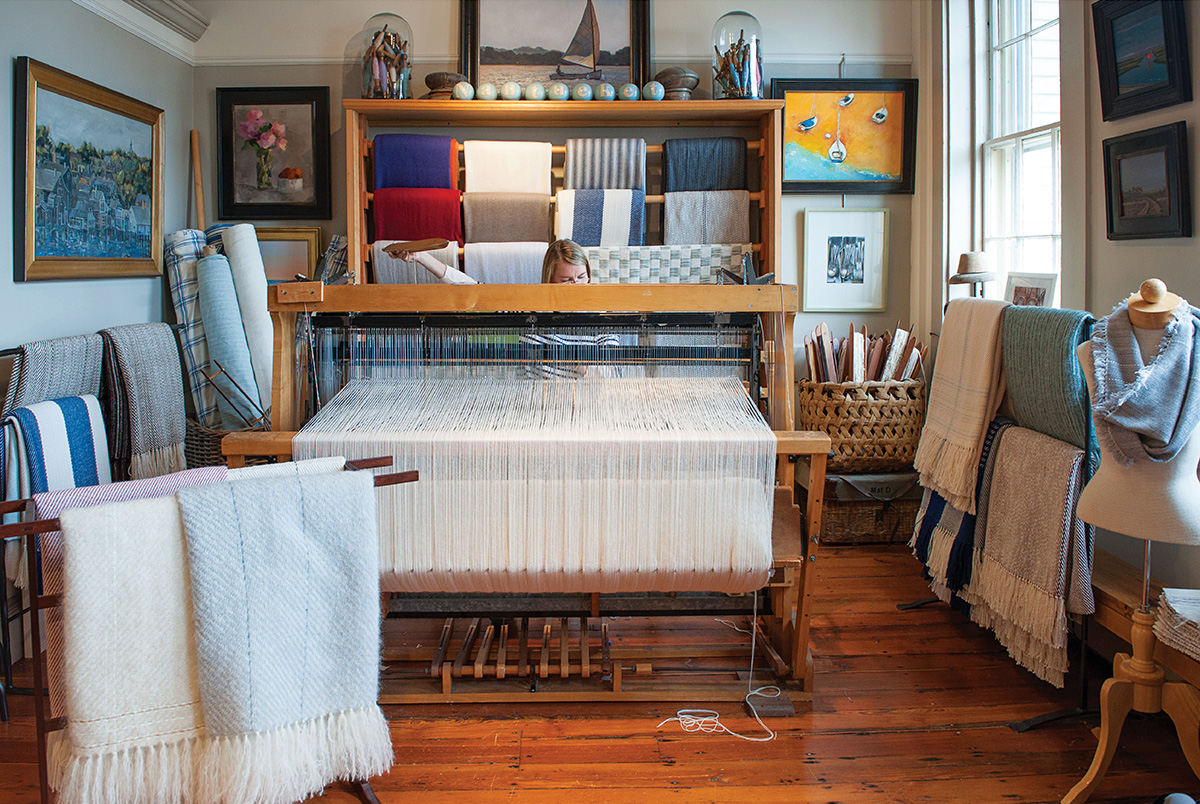
Peraner selects color palettes inspired by the Nantucket light and the surrounding architecture. / Courtesy Photo
Peraner believes quality fibers are crucial to creating high-end products. The mohair in Nantucket Looms’ popular blanket is sourced from South Africa, where the climate is optimal for Angora goats’ hair growth. The cotton throw, Peraner’s personal favorite, is made from durable cotton-flake yarn from North Carolina. Nantucket Looms’ alpaca fibers, naturally hypoallergenic and buttery to the touch, come from Peru. Cashmere is sourced from Southeast Asia, and silk is imported from Japan.
Through production, the weavers will touch every inch of the approximately 1,200 pieces made here each year. “When we weave, it’s kind of this simple, basic thing,” Peraner says. “But it’s also creating with these beautiful fibers this rewarding piece that someone’s going to cuddle beneath.”
Though their weaving methods haven’t changed since the 1960s, Peraner and her business partners, CEO Bess Clarke and head buyer Stephanie Hall, are constantly looking for new ways to update classic pieces. In the ’80s, geometric patterns, bold colors, and velvet accent threads and ribbons were all the rage. Current style has turned toward a coastal easiness, with which Peraner has always identified. For example, she says that the company’s cashmere throw—which for the past 15 years had been made with silk threads to achieve a sheen—is being redesigned. “Right now,” she says, “everything is very simplistic and elegant and monochromatic.”
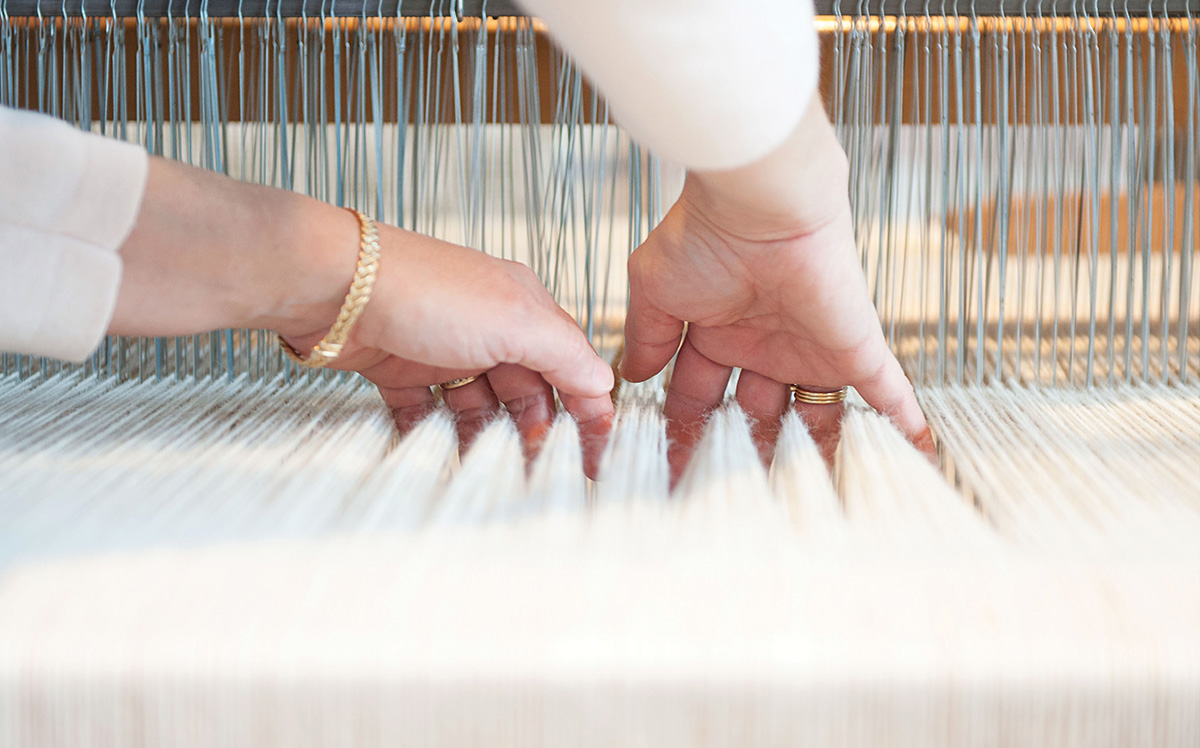
Peraner separates threads and checks their tautness before beginning to weave. / Courtesy Photo
Nantucket Looms stands by its pieces, and they repair throws that have endured the wear and tear of use. For many customers, it’s the heirloom quality of a piece that brings them back to the shop for repairs. “We’ll get throws back that have been woven in the ’70s and ’80s, and be asked to repair and bring them back to life,” Clarke says. “You’ll go up to the studio and see a dead, ratty blanky on a loom, but the customer would never think of getting rid of it. People will say, ‘I have a Nantucket Looms throw that my grandmother gave me when I was little, and I still have it.’”
At Nantucket Looms, business is grounded not just in product design and retail, but also in relationships. “It’s a way to live your life,” Clarke says. “It’s not just a pillow on your couch. It’s more: it’s a quality of life…. You can have one great blanket, and you use it every day, and it’s intertwined with the fresh air, and the beach, and the time with family and friends. There’s a value to it.”

Spools of fibers in an array of colors surround Brit Bennett as she works. / Courtesy Photo

Courtesy Photo
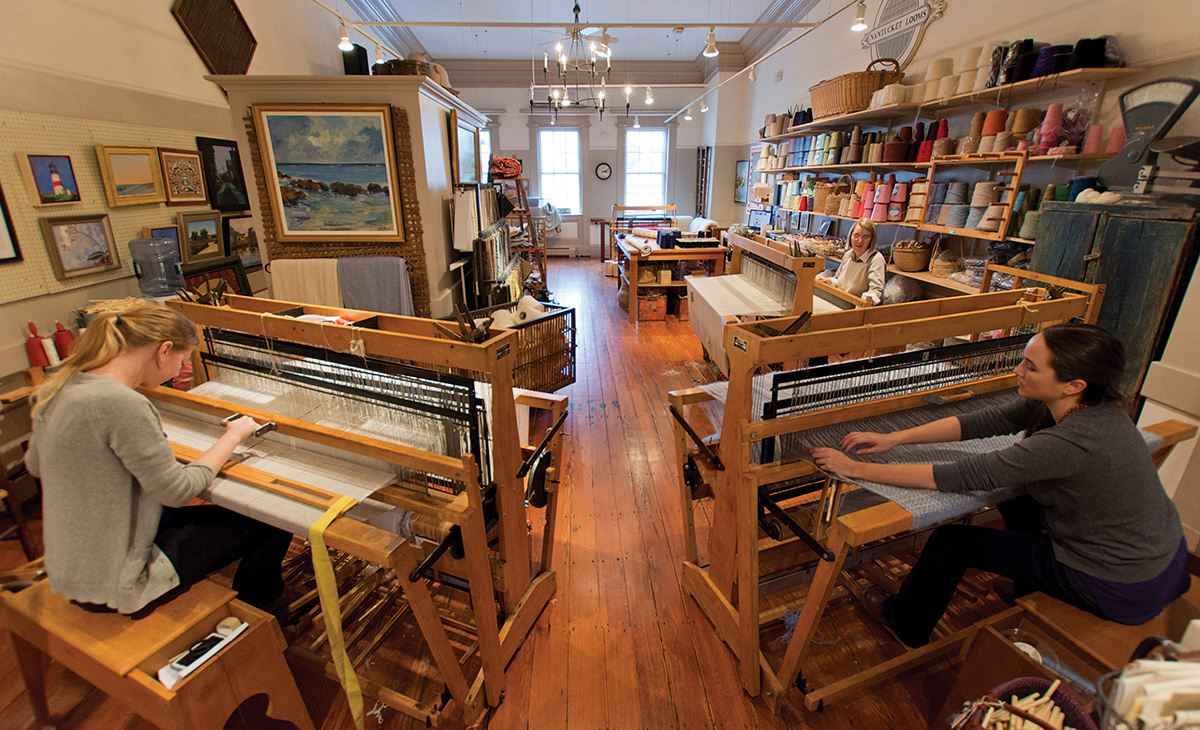
Courtesy Photo