Shirts So Good: Behind the Scenes at New England Shirt Company in Fall River
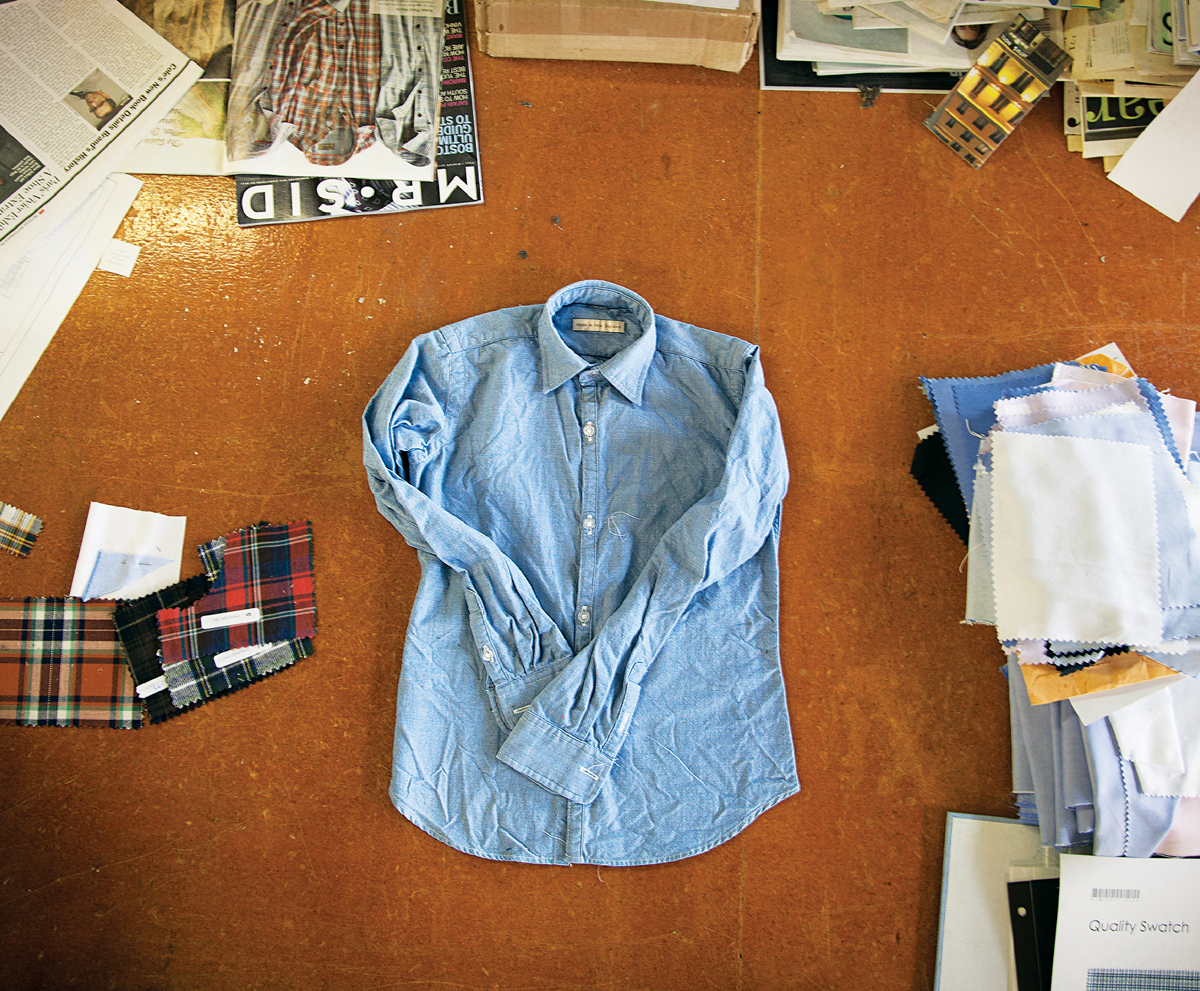
Photograph by Dana Smith
Even if invoking New York isn’t the quickest way to a Boston consumer’s heart, the ever-cool Brooklyn aesthetic tends to get a pass—especially when the product in question hails from our backyard. Case in point: the New England Shirt Company’s new William Gray line, inspired by that trendsetting borough to the south. The classic Oxfords and chambray button-downs embody a dapper look for the “dude who’s not required to wear a tie but does anyway—only he pairs it with a sports shirt,” says Joseph Snigier, operations analyst for the Fall River manufacturer.
That there are operations around for Snigier to analyze is a story in itself. Four years ago, Robert Kidder, then an executive at the Herringbone Shirt Company, learned the beloved textile mill where he worked would be closing. Not ready to call it quits, the industry vet bought the old mill and machinery and launched a line of limited-run dress and sports shirts under the New England Shirt Company moniker. “I wanted to prove it was still possible to make apparel in small factories in this country,” says Kidder, who lives in Ipswich. Since then, the brand has gained popularity, with boutiques here (such as Sault New England and Ari Boston) and across the country commissioning garments.
The company’s shirts all start as computer-aided-design (CAD) patterns printed on plotter paper. Fabric rolls from Europe are cut accordingly on a CNC machine, one of the only pieces of modern equipment in the 1883 mill. Pieces are bundled by size and dispatched downstairs for assembly. On the factory floor, different parts of the same top are put together simultaneously using a cellular-manufacturing technique: Rather than work on an assembly line, employees become adept at two or three different jobs (like making collars or attaching buttons or cuffs) and rotate through the sewing stations.
Given the area’s rich textile-manufacturing history, Snigier says there’s been no shortage of skilled workers or creative minds for the company’s ongoing product development. “This was traditionally the place to make garments,” he says. “We have families where the grandfather, the father, and the son were all involved in textiles. So we’re watching a constant evolution of people and industry in this little part of the world.”
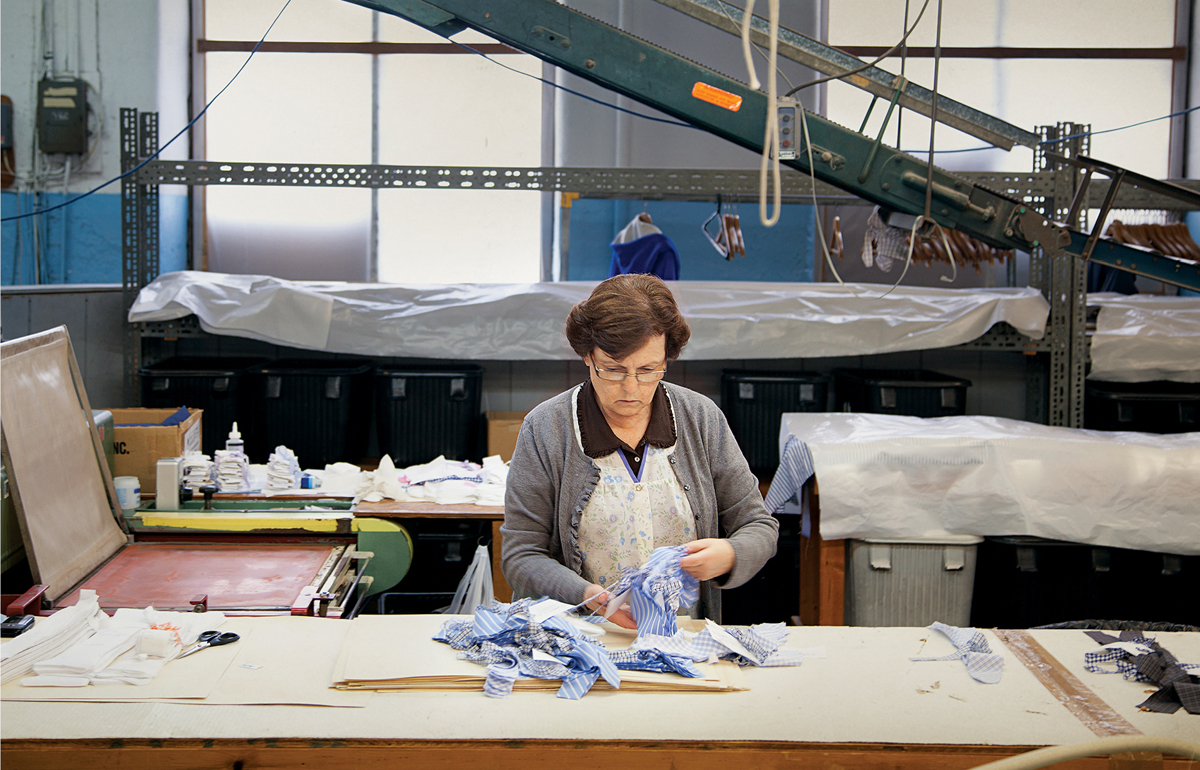
Photograph by Dana Smith
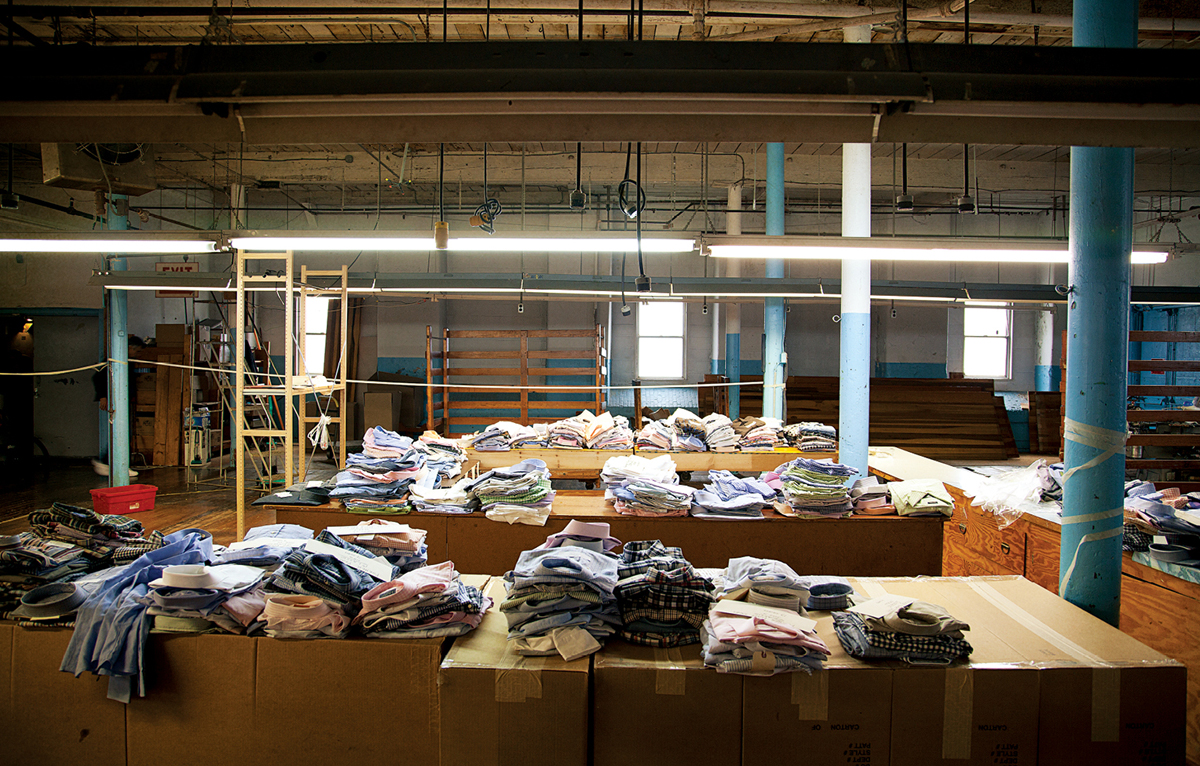
Photograph by Dana Smith
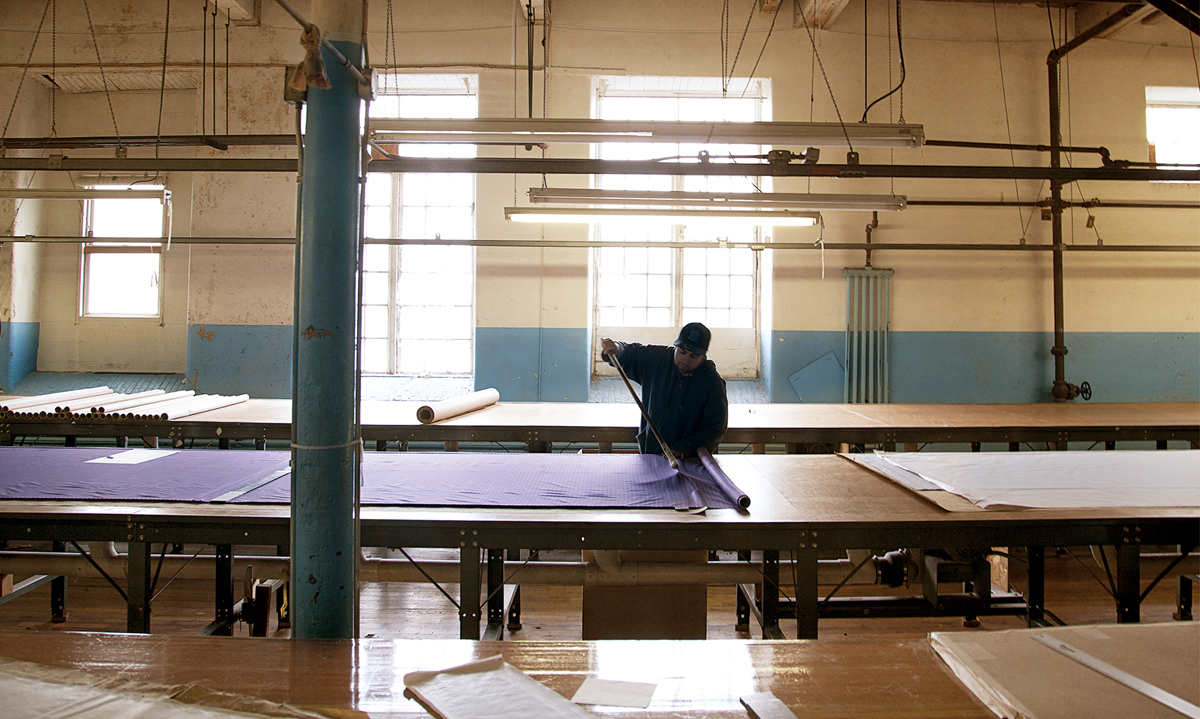
Photograph by Dana Smith
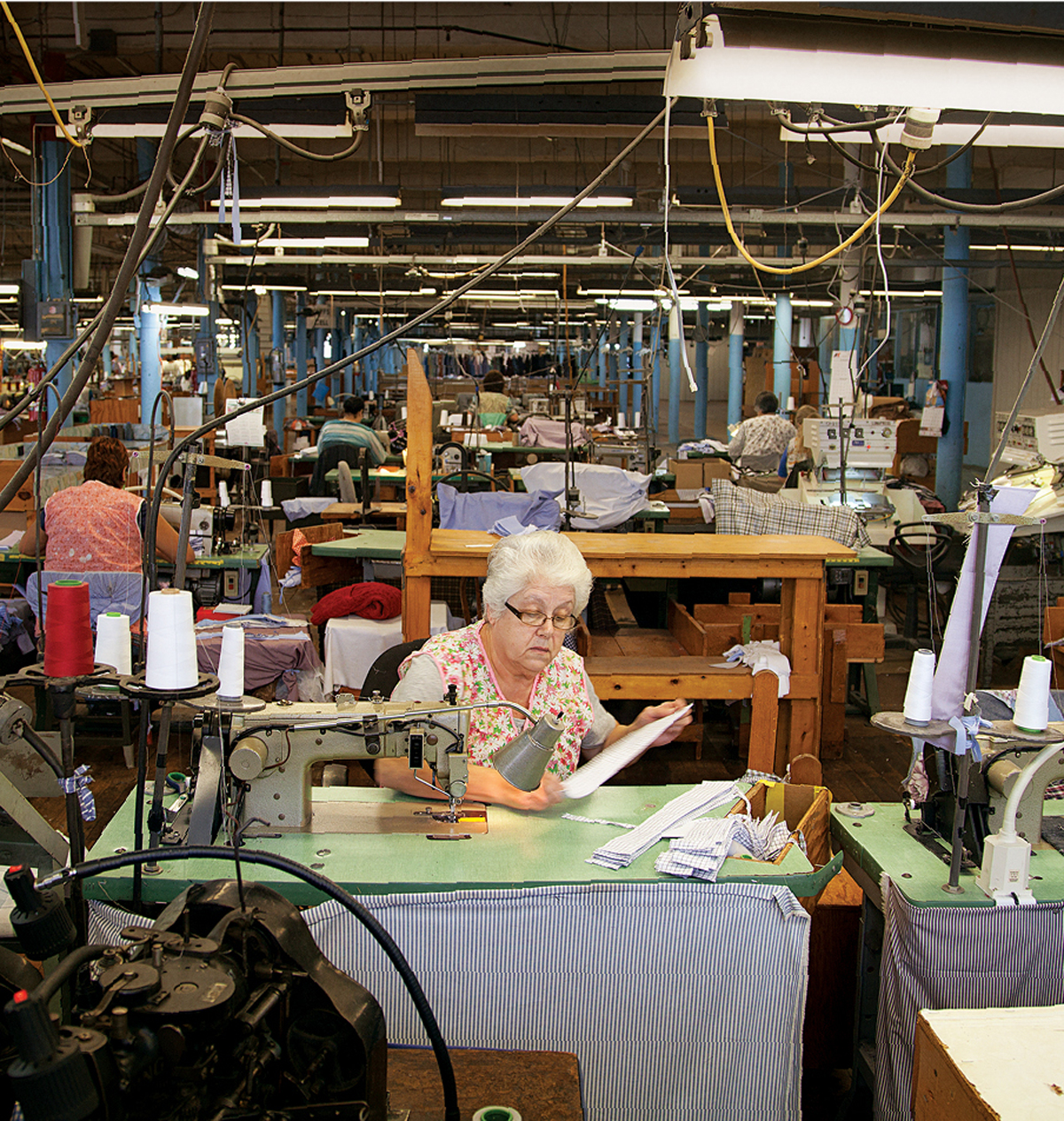
Photograph by Dana Smith
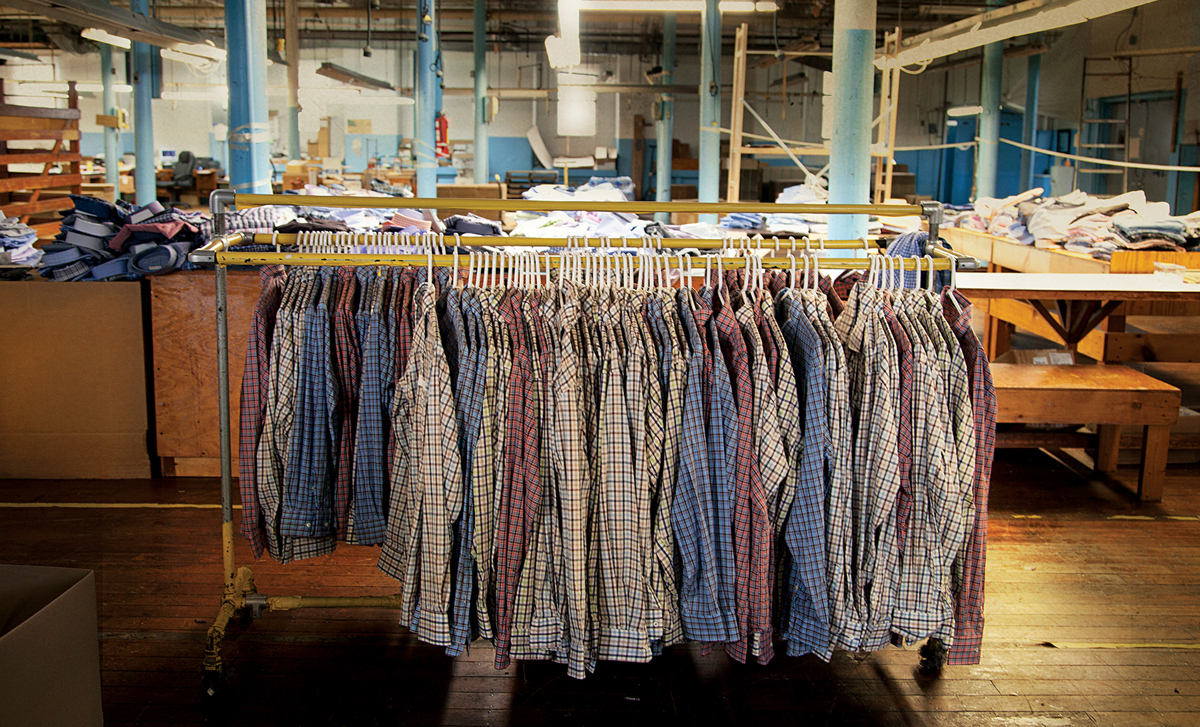
Photograph by Dana Smith