A Brand-New Kick
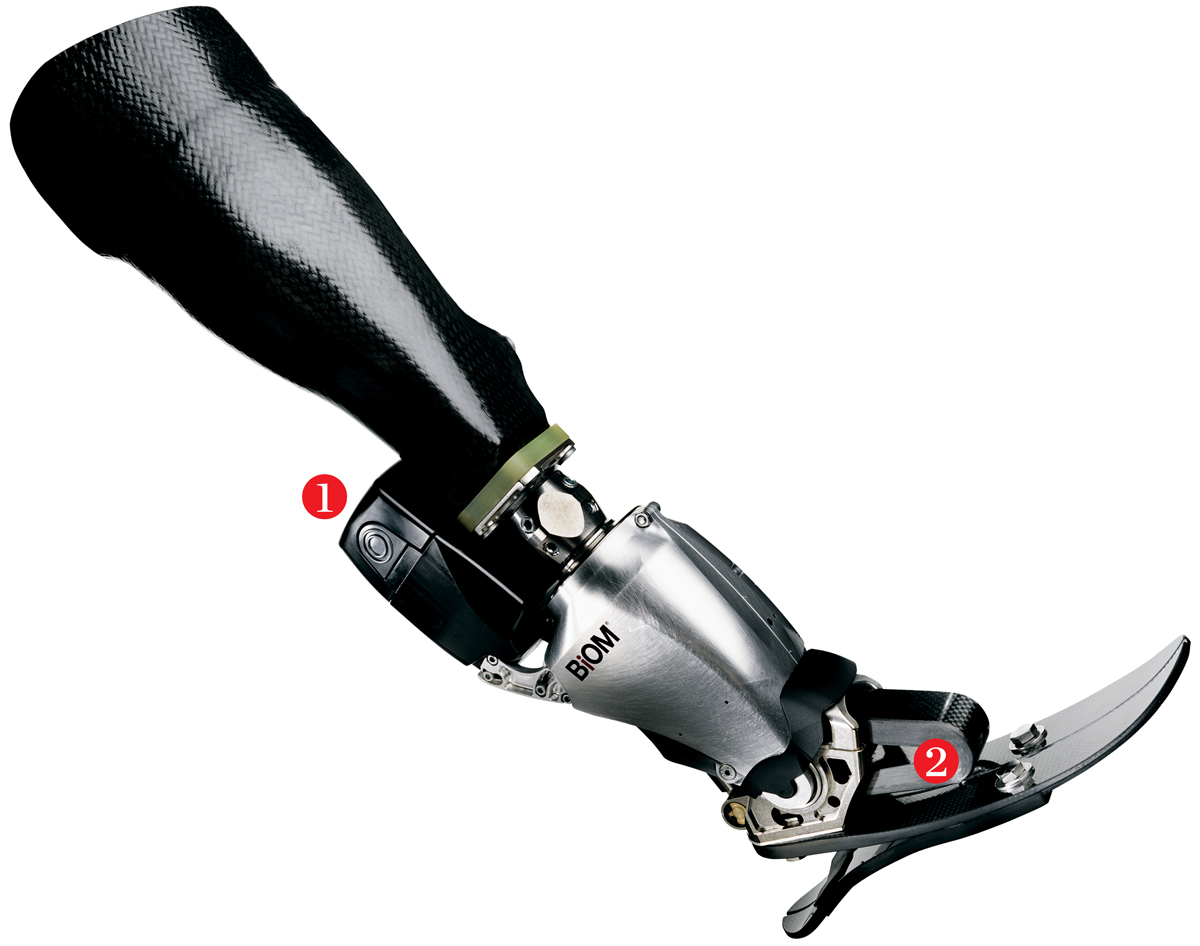
BiOM Breakdown. Here’s how the company’s first-of-its-kind powered ankle works: 1. Battery Pack: BiOM uses rechargeable batteries—not too different from the ones in your cell phone. Depending on the user’s weight and activity level, it takes one to three batteries to get through a day. The battery fits where the calf muscles would normally be, though the company hopes improved battery technology will allow for smaller, longer-lasting packs. 2. Carbon Spring: When you walk, your ankle muscles help propel you forward. This V-shaped spring simulates that oomph, providing just the right force at just the right moment to match a normal stride. (Continued below.) (Photograph by Bruce Peterson)
For those of us with two functioning legs, it’s easy to overlook the crucial role ankles play in walking. Every time we take a step, our Achilles tendons extend and contract and help power us forward. When amputees put on a standard carbon ankle prosthesis, they lose at least 50 percent of that propulsion. As a result, they typically can’t walk as fast or as far, and are more tired at the end of the day.
But a revolutionary new ankle prosthetic—produced by BiOM, a Bedford company founded on the breakthrough research of MIT professor Hugh Herr—is changing all that. BiOM’s motor-driven prosthesis replicates the power and function of a normal ankle. “We’ve had some people say to us it’s the closest thing they’ve had to having their leg back,” says Matt Albuquerque, president of Next Step Bionics & Prosthetics, which sells the ankle. “That had been something I’ve never heard before.”
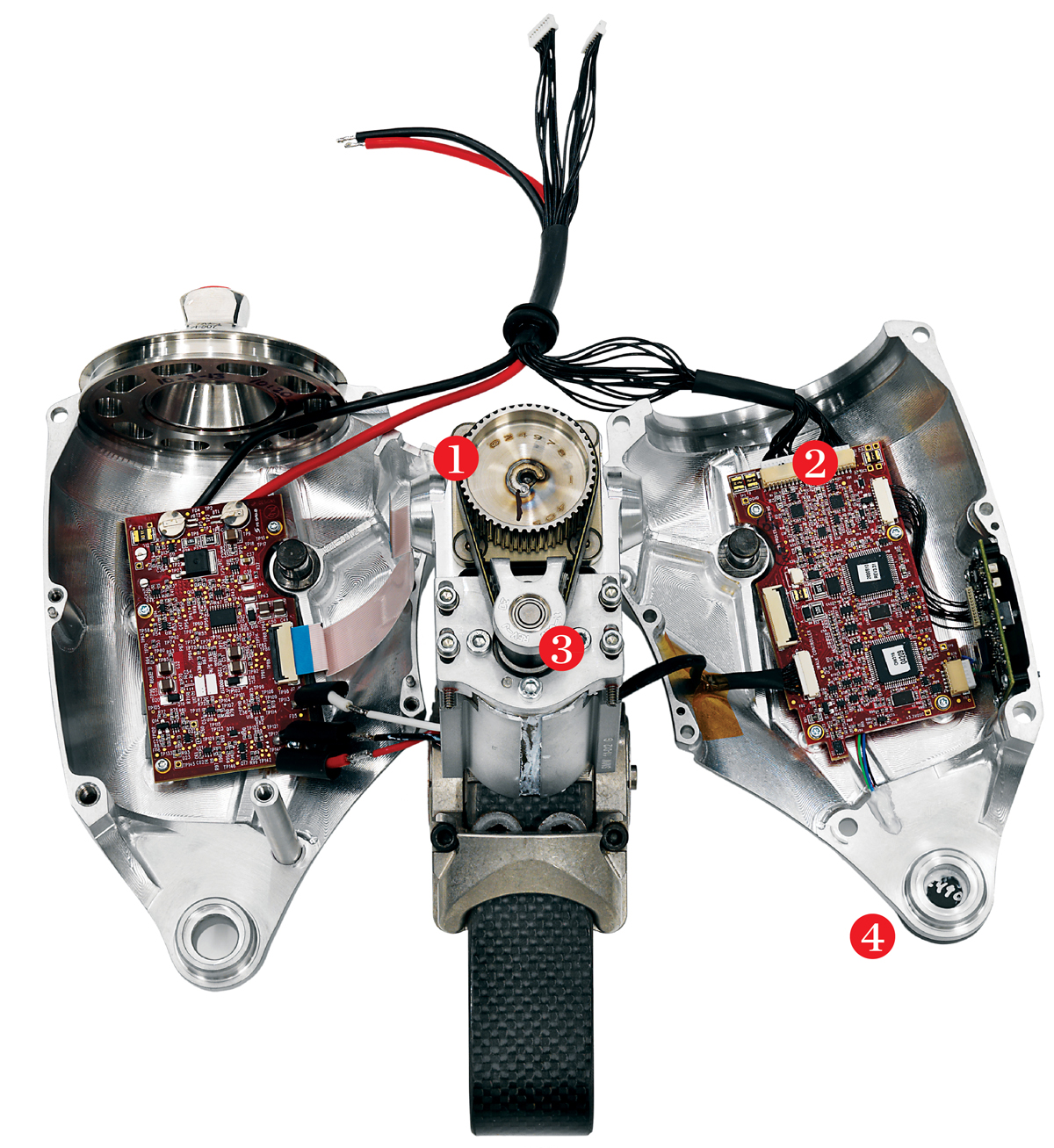
BiOM Breakdown. (Continued from above.) 1. Ball Screw: Its pumping replicates the Achilles tendon. In effect, it loads and powers the carbon spring. 2. Microprocessors: This is where the magic happens: Four microprocessors run complicated algorithms that take into consideration the user’s height, weight, stride, and gait (are you a heel striker, or do you usually land on your midfoot?) to determine just how much force to power through the ankle at any given moment. 3. Motor: This is what makes it all go—transferring energy from the battery to drive the ball screw and, in turn, the carbon spring. 4. Main Sensor: Sensors determine how the BiOM ankle is positioned at any given moment: Is it in the air? On the ground? Is the user up on his toes? Or resting on his heels? With that information, the prosthesis can determine how much power to provide to the spring to simulate normal ankle function. (Photograph by Bruce Peterson)
The BiOM ankle, though, still has one big problem: It’s “prohibitively expensive,” Albuquerque says. At about $50,000, it costs up to $40,000 more than a standard prosthesis, and isn’t covered by Medicare, Medicaid, or most insurers. That means most amputees can’t afford it. BiOM has sold about 1,000 units since it launched the product in 2011, and most of its customers have been veterans, covered by the Department of Defense or the Veterans Administration. (DoD money funded Herr’s research and helped BiOM get off the ground.)
Insurance coverage of all prostheses is inconsistent, even though advocates point to research showing that having a prosthesis decreases long-term healthcare costs by keeping amputees more active and helping them avoid issues like obesity, diabetes, and depression.
BiOM CEO Tim McCarthy goes further: The company’s new ankle, he says, also alleviates stress on muscles that are forced to overcompensate for the missing ankle propulsion. “Our mode of transportation is going to save the healthcare payer millions of dollars because we’re going to reduce back pain, hip pain, knee pain. We’re going to improve cardiovascular health and all those costs that are associated with those comorbidities,” he says.
“I think it is a reasonable argument,” says Tom Fise, the executive director of the American Orthotic & Prosthetic Association, noting that it builds off the same principle as previous studies. Is there enough data to convince Medicare and Medicaid officials to cover the BiOM ankle? The company will find out soon—at press time, BiOM was awaiting a ruling. If government insurers give it a thumbs up, private insurers will likely follow suit.
In the meantime, McCarthy says his company will continue innovating. A new powered knee prosthesis is three to five years away. “We’re going to focus on foot-ankle,” he says, “and then we’ll work our way north.”
WHAT’S NEXT?
Here are a few projects in development in Hugh Herr’s Biomechatronics group at the MIT Media Lab. Researchers believe they could reach consumers in two to five years.
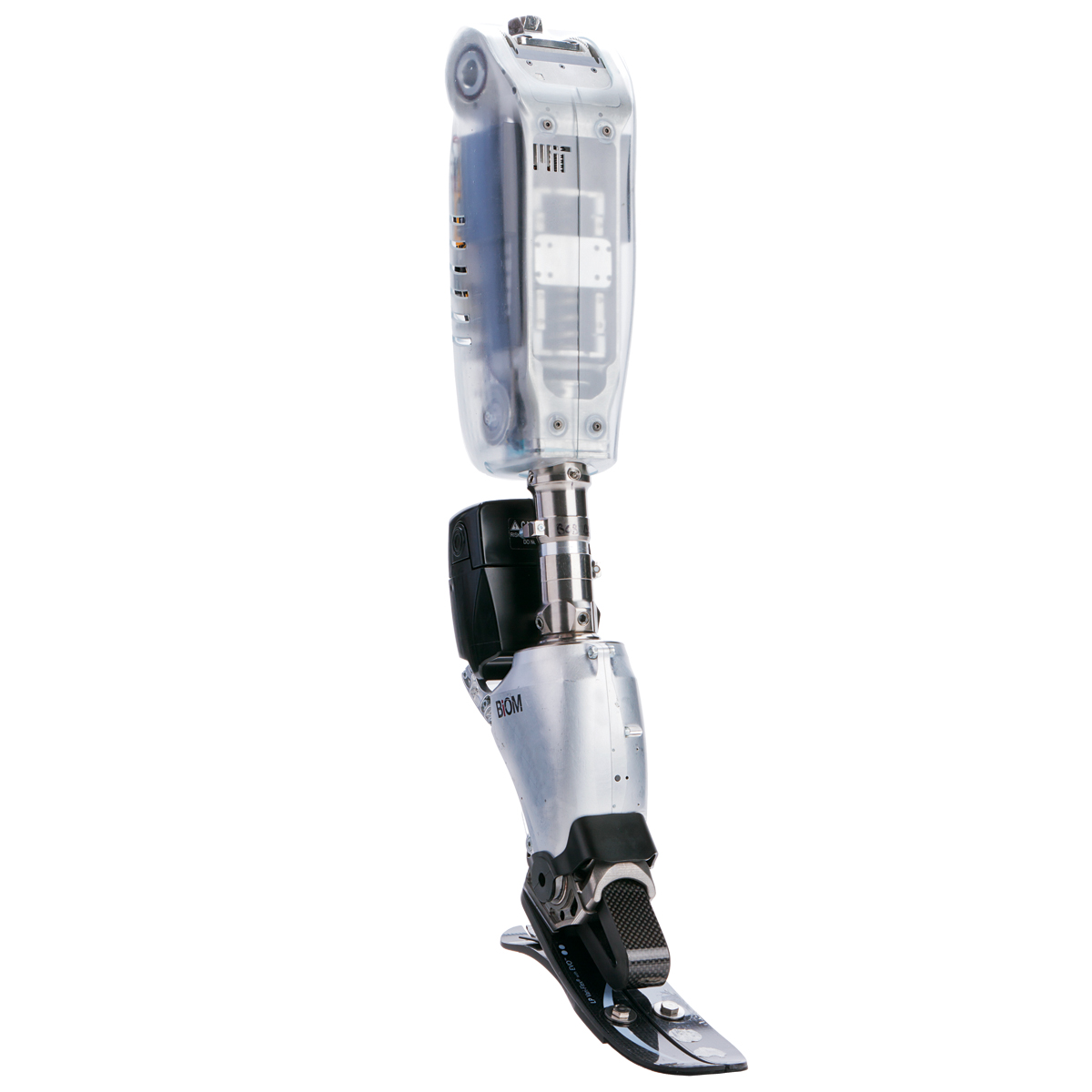
Photograph by Chris Conti
Knee Prosthesis
Most prosthetic knees available right now aren’t powered. This one, though, re-creates the power and energy of a biological knee. Designed to be efficient, the knee draws on battery power only when necessary and, like a hybrid car, is capable of recharging its battery when you walk.
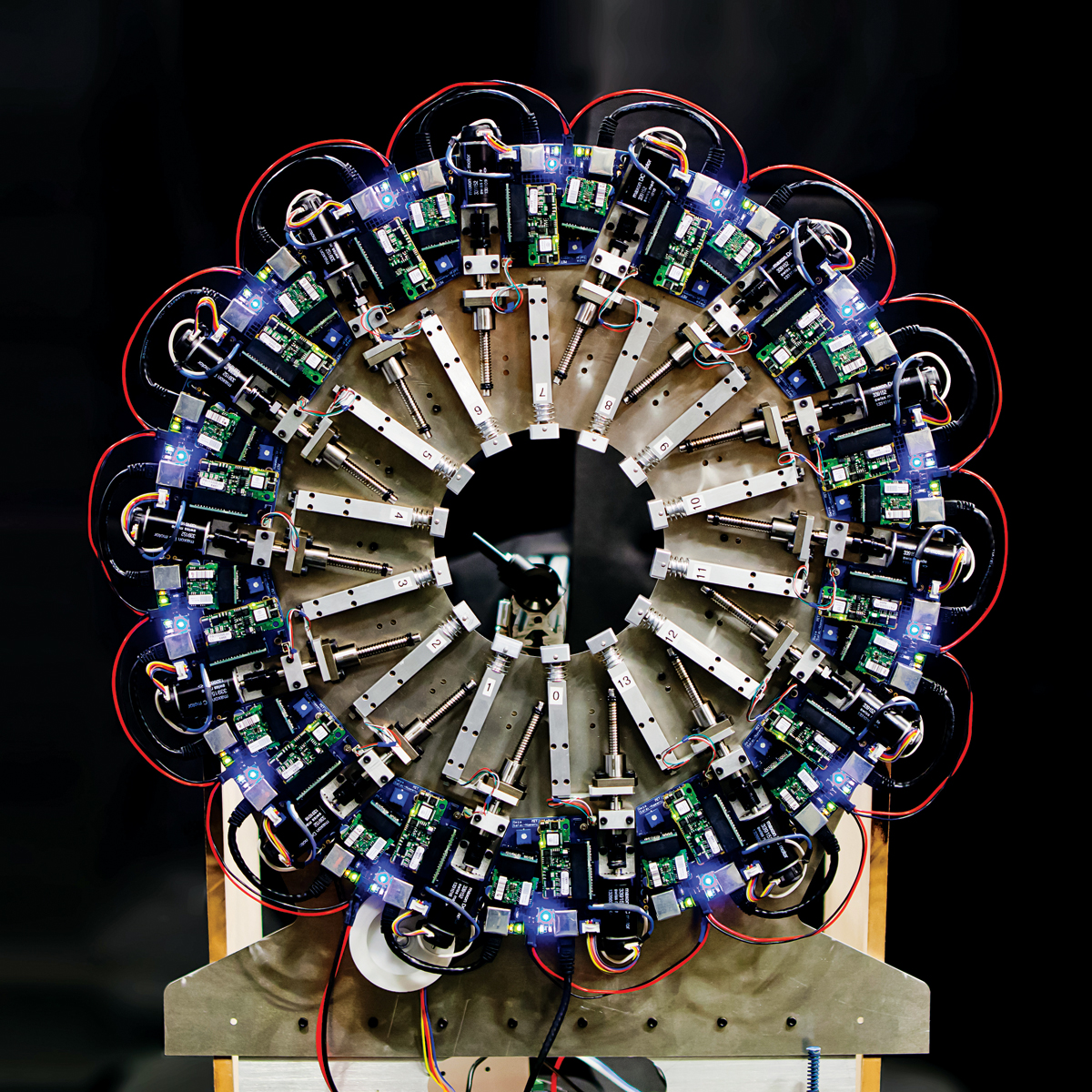
Photograph by Chris Conti
Fit Socket
Comfortably fitting a prosthesis to a limb remains a huge challenge. This device is designed to help fix that: Users insert their limb to precisely measure its shape and even the stiffness of the skin around it, so a socket—the limb-prosthesis connector—can be mapped accordingly.
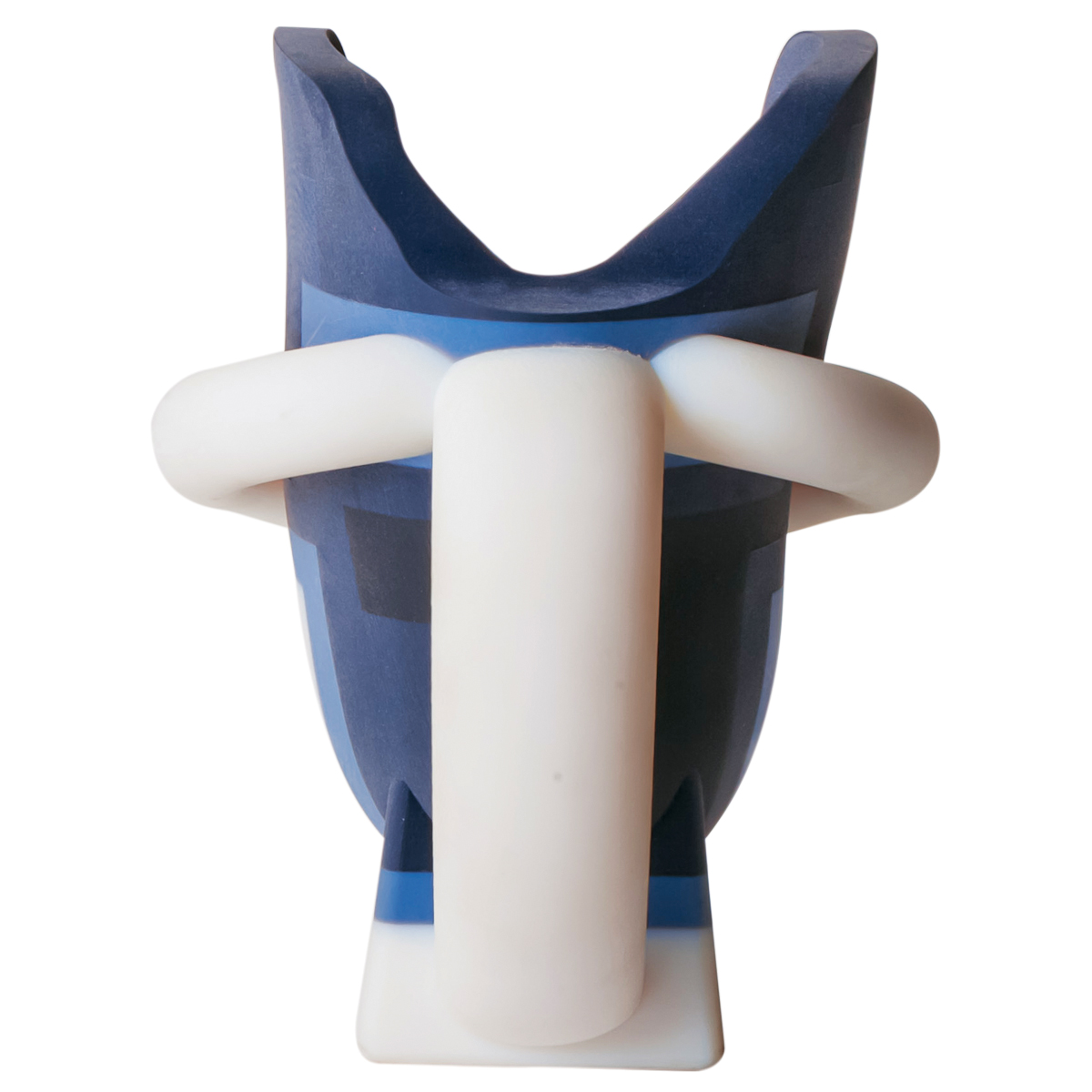
Photograph by Chris Conti
3-D-Printed Socket
Currently, sockets are fashioned by hand: The process is slow, expensive, and difficult to replicate. But Herr’s group is automating it. They take the data from the Fit Socket and quickly and relatively cheaply pump out precise, replicable, and more comfortable sockets from 3-D printers.