Happy Feet
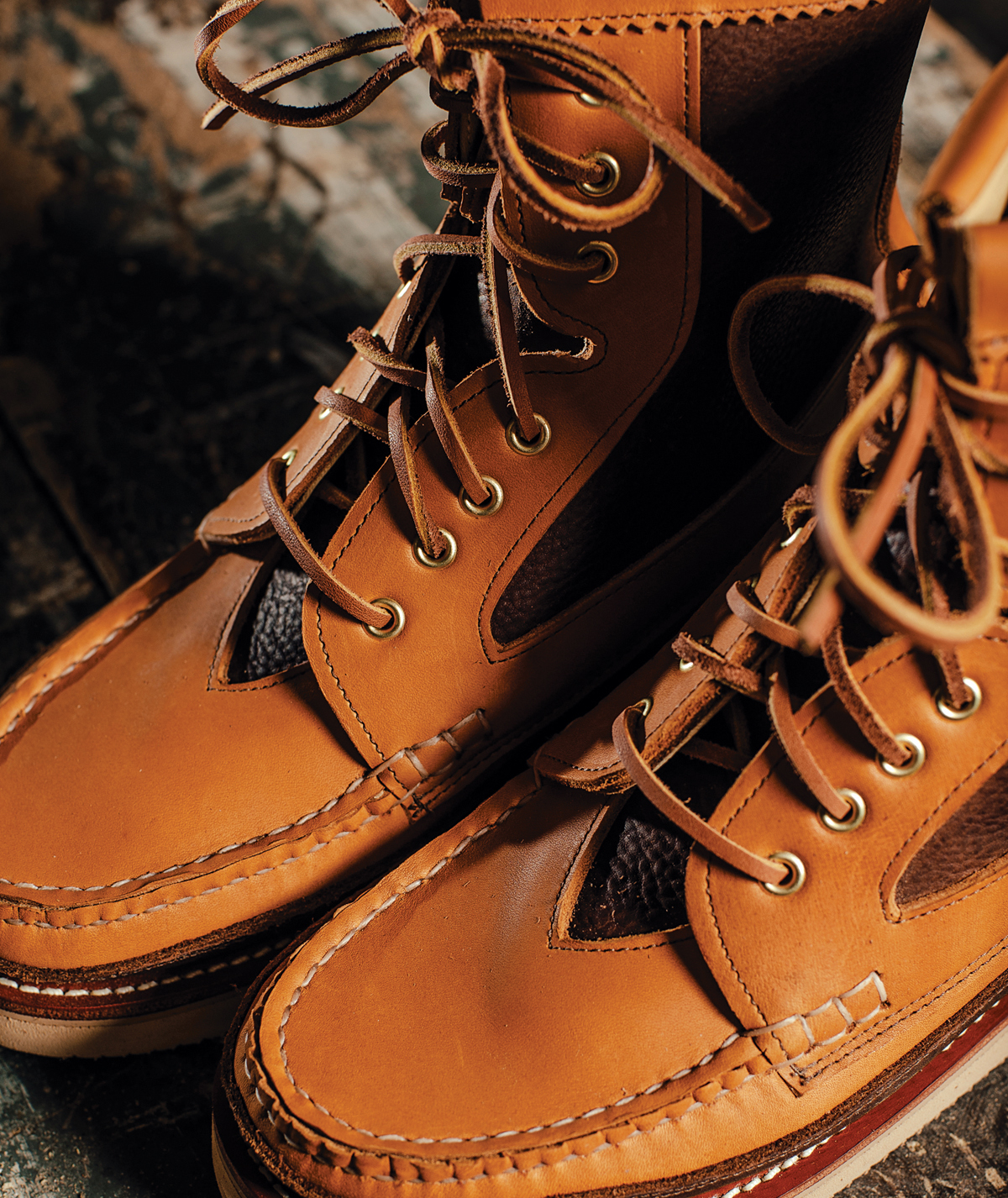
Photograph by Mark Fleming
Dan Heselton and Greg Cordeiro met in a breakfast club of sorts. The two men—both Timberland employees at the time—first crossed paths in the wee hours of the morning at a shoemaking workshop offered by a coworker. The pair became fast friends, bonding over their passion for the craft. One night over beers they discovered they had something else in common: Both had drafted detailed plans to start handmade-footwear companies in an effort to join the growing movement to bring manufacturing back home. Their shared vision was all they needed to put a plan into action.
Before launching their company, New England Outerwear, the duo apprenticed with moccasin craftsmen in Maine. “That really focused our vision and gave us the skills we needed to understand construction and the processes used for true handsewn shoes,” Heselton says. Next they acquired a few antique sewing-and-cutting machines and set up shop in a converted barn in Lewiston, Maine, bringing in a handful of skilled artisans to masterfully handcraft timeless moccasins, boat shoes, and boots. For inspiration, they studied classic styles from the early to mid-1900s, “when L. L. Bean was just starting out and there were a million small moccasin makers all over the Northeast,” Heselton says.
When it comes to crafting their own footwear, Heselton and Cordeiro use only the finest materials, including Horween leather (used by the NFL for footballs since the early 1940s). The process begins with a shoemaker tracing a paper pattern onto the hide before cutting it by hand. Some pieces are stitched together with single- or double-needle industrial sewing machines, while others are painstakingly handsewn with threads sourced from a nearby distributor. Employees then attach either high-performance Vibram soles or another sturdy soling material with adhesive from New Hampshire’s Worthen Industries before the shoes get stitched again for reinforcement. “A boat shoe can take an experienced handsewer 10 to 20 minutes,” Heselton says, “but a crepe-wrapped shoe takes upward of an hour.” Metal hardware from Danvers, Massachusetts, is added by hand. “Ninety-five percent of what we use is domestically sourced,” Cordeiro says. “We start in New England and spread our feelers out from there.”
For Heselton and Cordeiro—who grew up on the North and South Shore, respectively—keeping the tradition of New England fabrication alive was an important factor in their decision to go into business. “This idea of bringing manufacturing back is called a trend right now, but I think it’s here to stay,” says Cordeiro, citing Apple’s forthcoming Mesa, Arizona, factory and a rumored Nike plant in Colorado that may be in the works. “People in this country are really starting to educate themselves on where their money is going, and those who do are willing to spend a little more on something they care about—and to support their neighbor,” he says, “rather than buying something that will fall apart in a year.”
Since debuting their spring 2014 collection this past summer, more than three dozen retailers have placed orders with the company, including some as far away as Japan, Scotland, and Italy. Locally their kicks have been spotted in boutiques such as Sault New England, the Boston outpost of the Tannery, and Thistle Hill, in Rockport, and the duo say they’re now looking at production numbers of 200 pairs a month and growing. With a full-time staff of only 10 people, it’s an impressive feat, indeed.
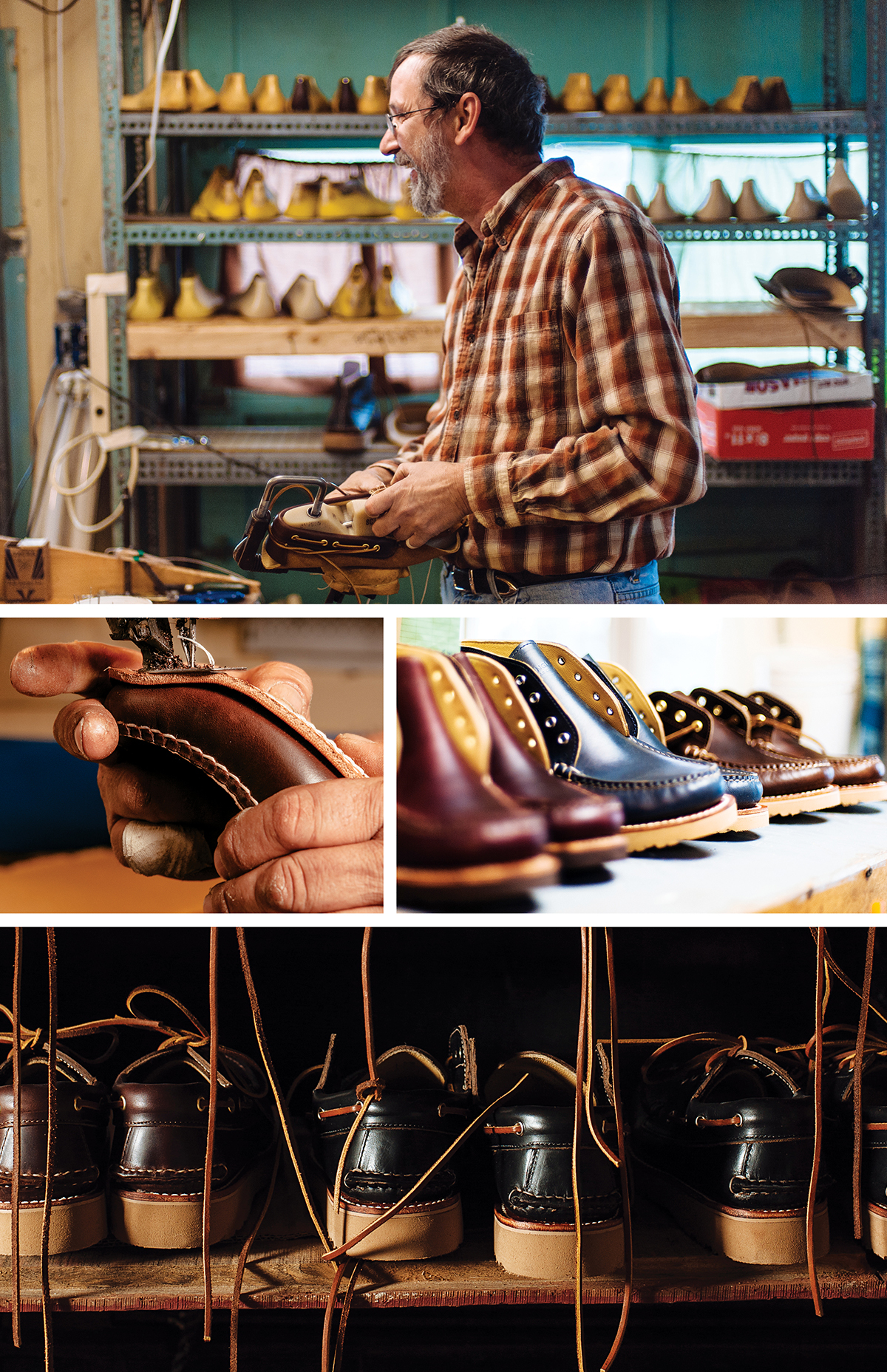
Photographs by Mark Fleming
From top, an employee sews a shoe by hand, shoes in progress, boat shoes await their final cleaning and finishing.
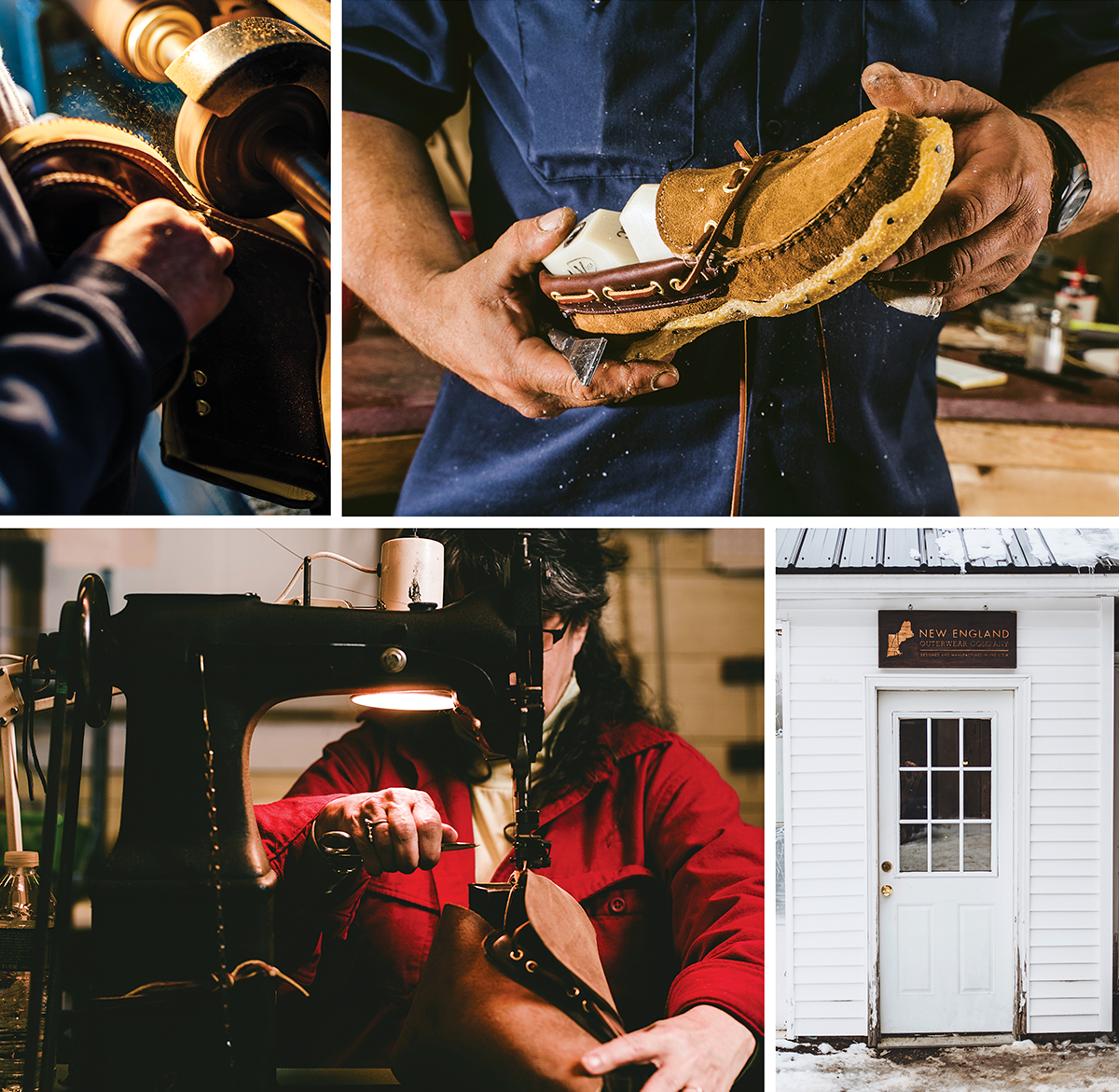
Photographs by Mark Fleming
Clockwise from top left, the footwear finishing process includes cutting, sanding, and buffing the soles; one of the company’s signature moccasins; New England Outerwear’s headquarters, a stitcher affixes the upper of a boat shoe to the collar using a post-bed sewing machine.
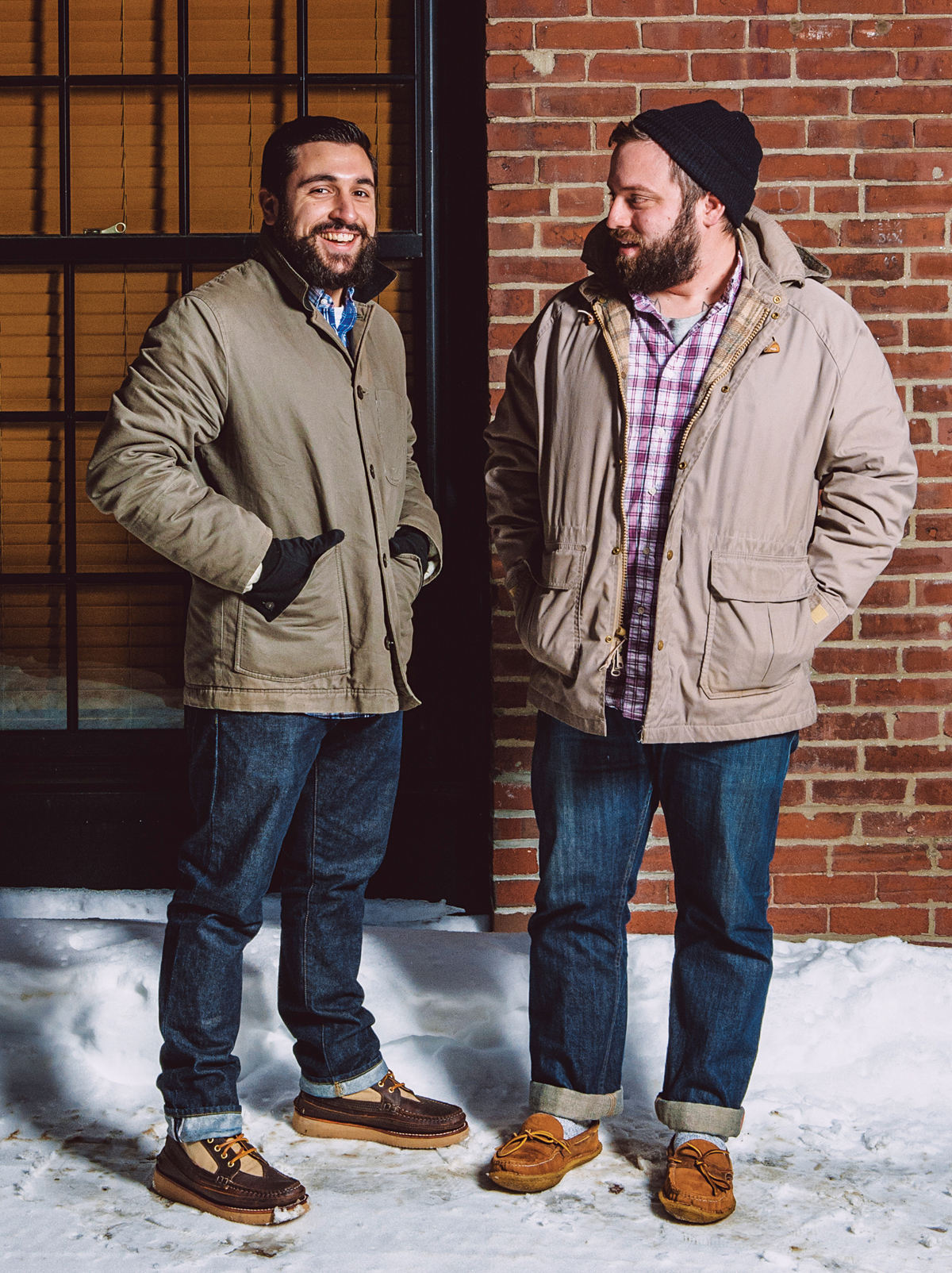
Photograph by Mark Fleming
Cordeiro (left, wearing “Harvesters” boots) and Heselton (right, sporting the crepe-wrapped “Overcast” moccasins) in downtown Lewiston, Maine.
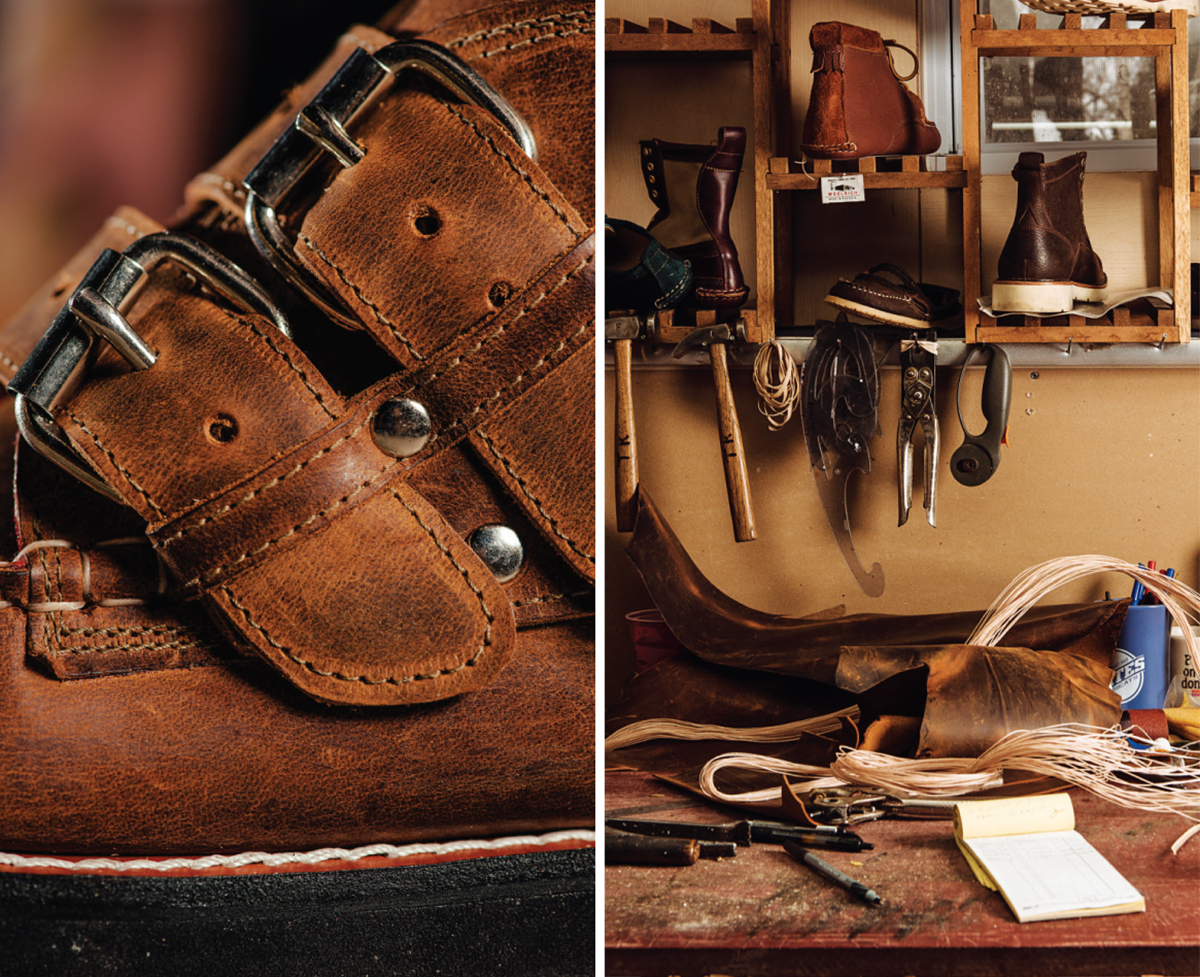
Photographs by Mark Fleming
From left, a new footwear style for men and women; a handsewers’ bench in the workshop.
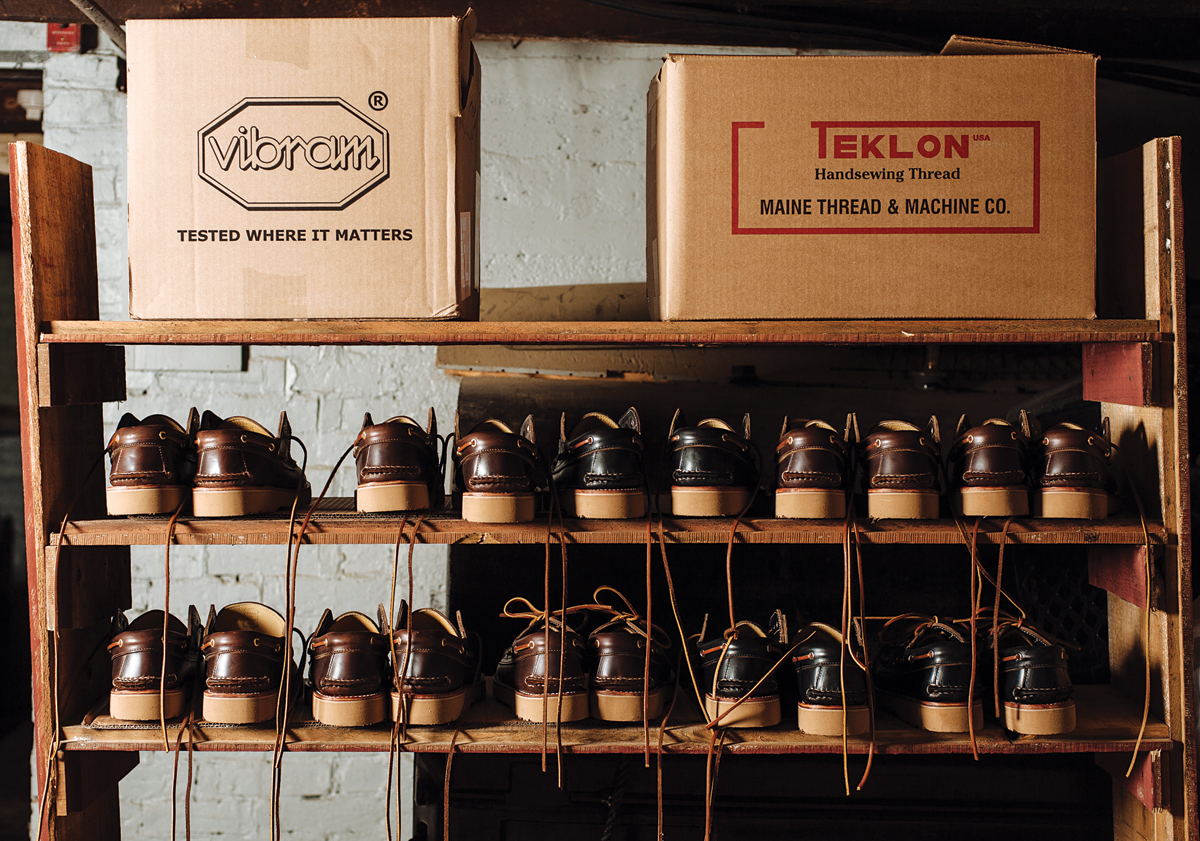
Photograph by Mark Fleming
The company sources materials locally whenever possible. Heavy-duty Vibram soles are from Concord, while the thread for handsewing comes from Lewiston, Maine, where the factory is located.