Pot Luck: Myrth Ceramics Creates Timeless Stoneware
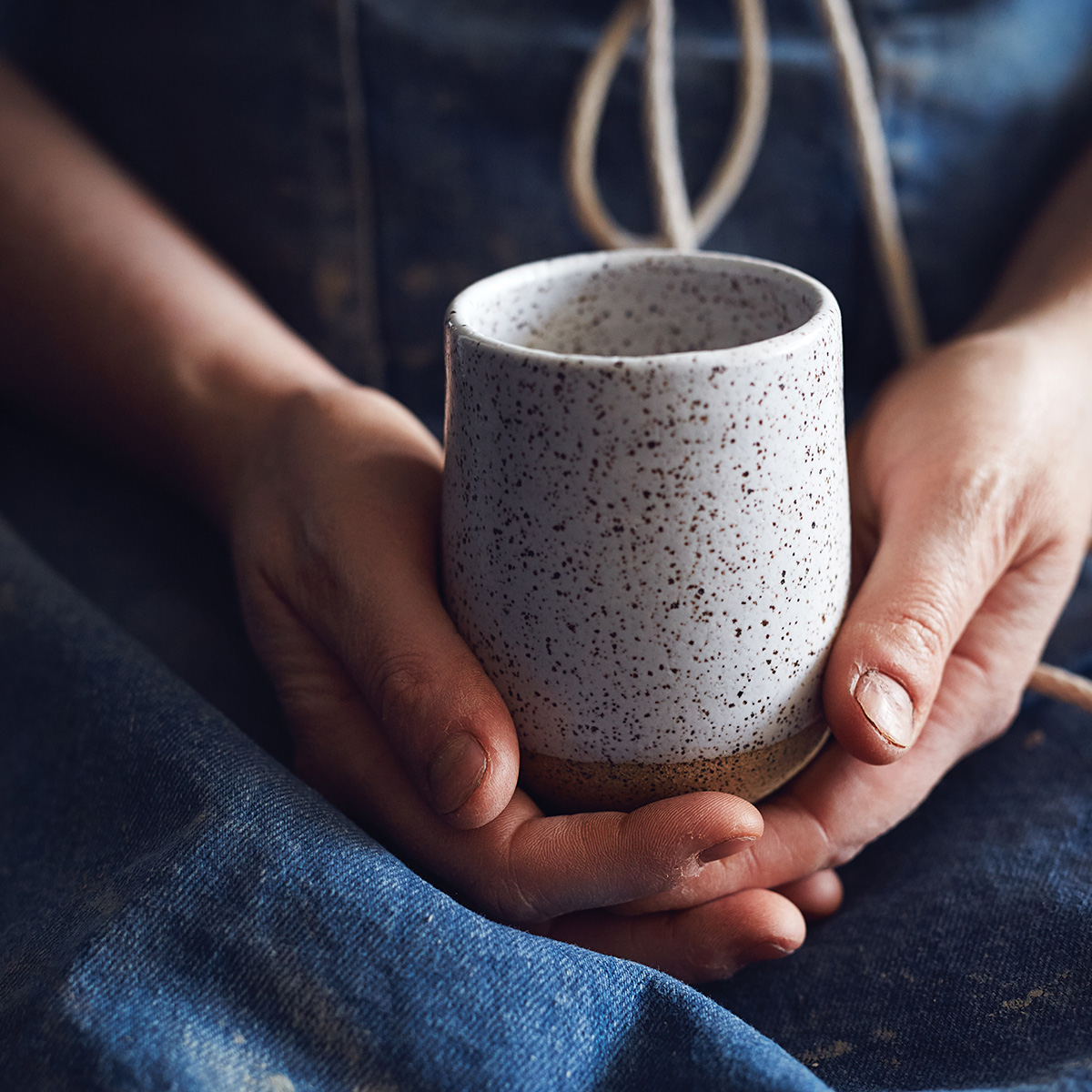
Photograph by Pat Piasecki
It all started with a glass of sherry. Holed up in Barcelona Wine Bar’s newly opened South End outpost in 2014, longtime potters Abby Smallwood and Beth Connolly sipped Spanish wine and rehashed their shared dream of opening their own studio. “We always talked about having our own place,” says Abby, who’d met Beth in a pottery class six years earlier. That night at Barcelona, “We said, ‘Let’s just do it. Let’s find a place and do it.’” Within a week, the two friends—along with Abby’s husband, Eric—signed a lease for a sunny workspace in Allston, and Myrth Ceramics was born.
The small pottery outfit gets its name from the word “mirth,” chosen for its expression of warmth and happiness. It’s a sentiment the team has embraced as it’s developed the line of handmade stoneware, which includes everything from neutral-toned vases and planters to speckled tumblers and serving bowls. “The greatest compliment we’ve gotten is, ‘When I look at your work, it makes me calm,’” Abby says. “That’s exactly what we’re going for with our pieces. We want them to live in happiness and bring you happiness in our kind of calm, natural way.”
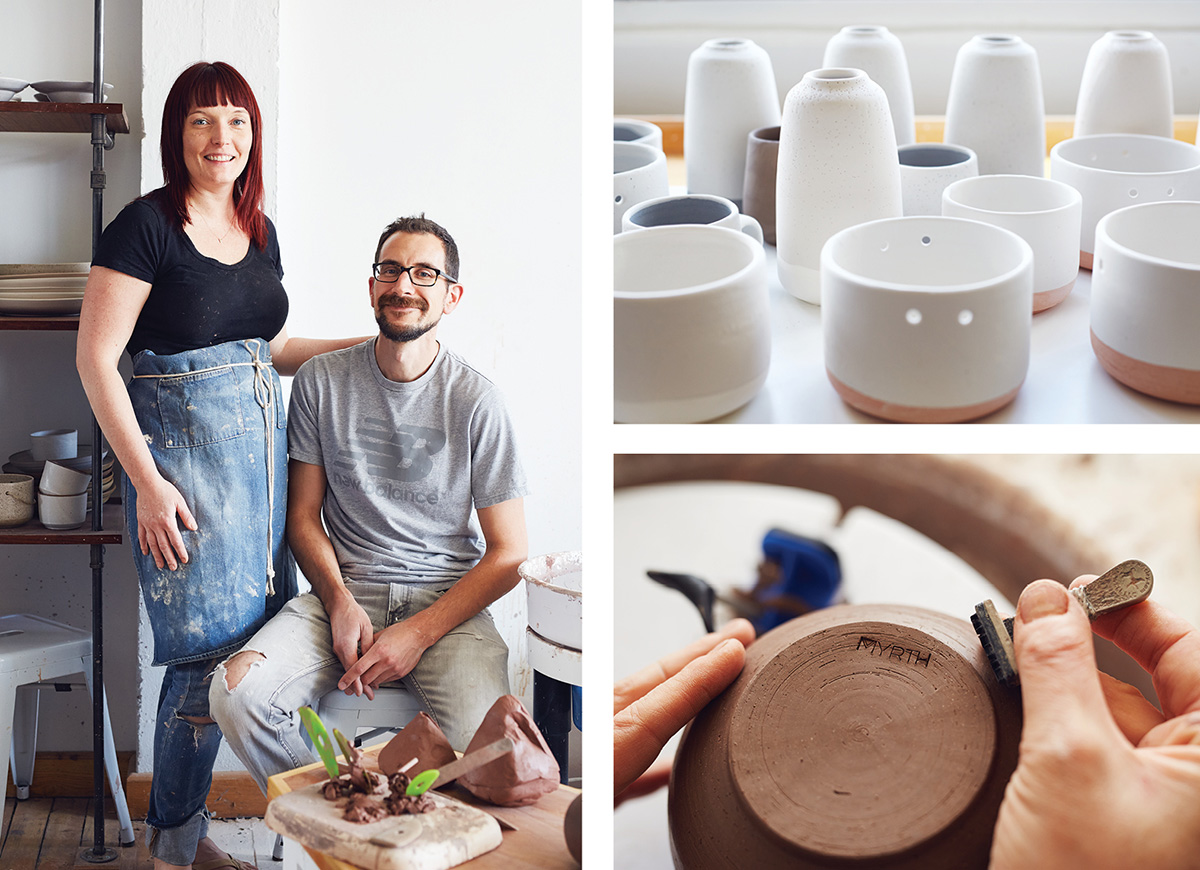
Clockwise, Abby and Eric Smallwood in their Allston studio; bisque-fired pieces are finished with house-made glazes before being returned to the electric kiln for a second, hotter firing; fresh off the wheel, a vessel is stamped with the Myrth Ceramics logo. / Photographs by Pat Piasecki
Described by Eric as “simple and modern,” all of Myrth’s pieces are designed and crafted by the Smallwoods (Beth has since left the company) in their second-floor studio on Braintree Street. Each vessel begins as a chunk of stoneware clay, which—in a process similar to kneading dough—the potters “wedge” to ensure even moisture content and density. The prepared clay is then slammed onto a wheel and manipulated, or “thrown,” into shape. Once the vessel is formed, the potters trim it to add detailing, brand the bottom with the company logo, and place it on carts to dry for several days. Dried pieces, known as greenware, are then “bisque fired” in an electric kiln at a whopping 1,828 degrees. Now in the bisqueware phase, the vessels are glazed and treated to a second, hotter spin in the electric kiln. It’s a laborious process: Because of the lengthy drying and firing periods, creating a single piece from start to finish can take as long as a week.
Logging that kind of studio time has been a labor of love for the Smallwoods, both of whom have full-time jobs outside of Myrth Ceramics: Abby is a materials designer for New Balance, and Eric is a freelance product designer. Back in their pottery-class days at Boston’s Cyclorama, the couple bonded with Beth over their love of the craft and admiration for their mentor, potter Darrell Finnegan. “He’s an absolutely amazing teacher,” says Abby, pointing to a picture of Finnegan near the door in the company’s Allston studio. “He taught us everything we know.”
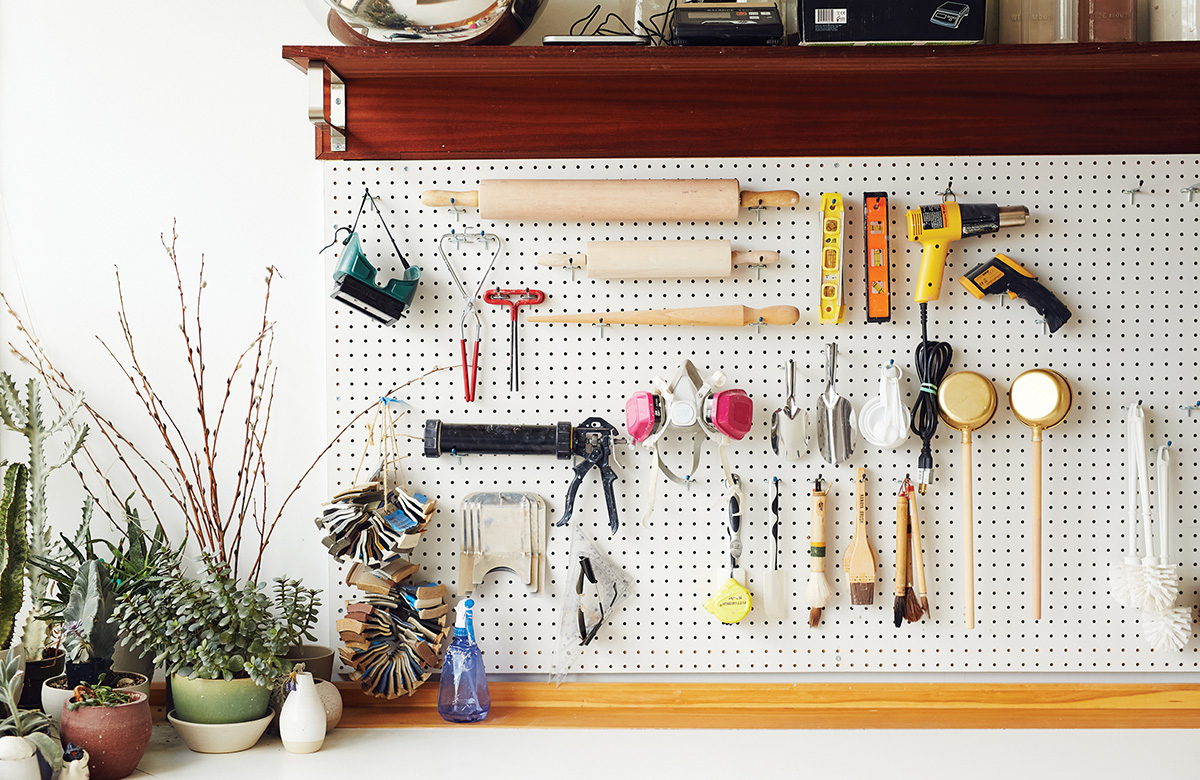
The potters use a variety of tools to shape, glaze, and fire their pieces. “It’s all about experimentation,” Abby says. / Photograph by Pat Piasecki
As Myrth Ceramics wraps its second year of production, it’s clear that this combination of passion and expert mentorship has paid off. The company’s goods (which range in price from $32 to $650) are now carried by numerous local businesses, from the South End’s Olives & Grace to the Boston-based online retailer Covet+Lou. Kimberly LaFoy, co-owner of Somerville’s Loyal Supply Co., also stocks Myrth Ceramics pieces, including a stoneware match striker crafted exclusively for her store. “I love the form and function of the simple shapes that they design and create,” she says. “Being able to see their process and their beautiful space was really inspiring.” Requests for collaboration have poured in from other local businesses, too. In addition to orders from Lynzarium’s Plant Shack, in Gloucester, and the Rockport bakery Mayflour Confections, the Myrth Ceramics team recently partnered with chef and restaurateur Barbara Lynch on a line of tableware for her Italian eatery Sportello.
“Darrell has always said to us that a piece is not finished until it’s in its home. That’s such a huge part of what we do,” Abby says. “It’s so rewarding to hear how a vessel has changed a client’s space.”
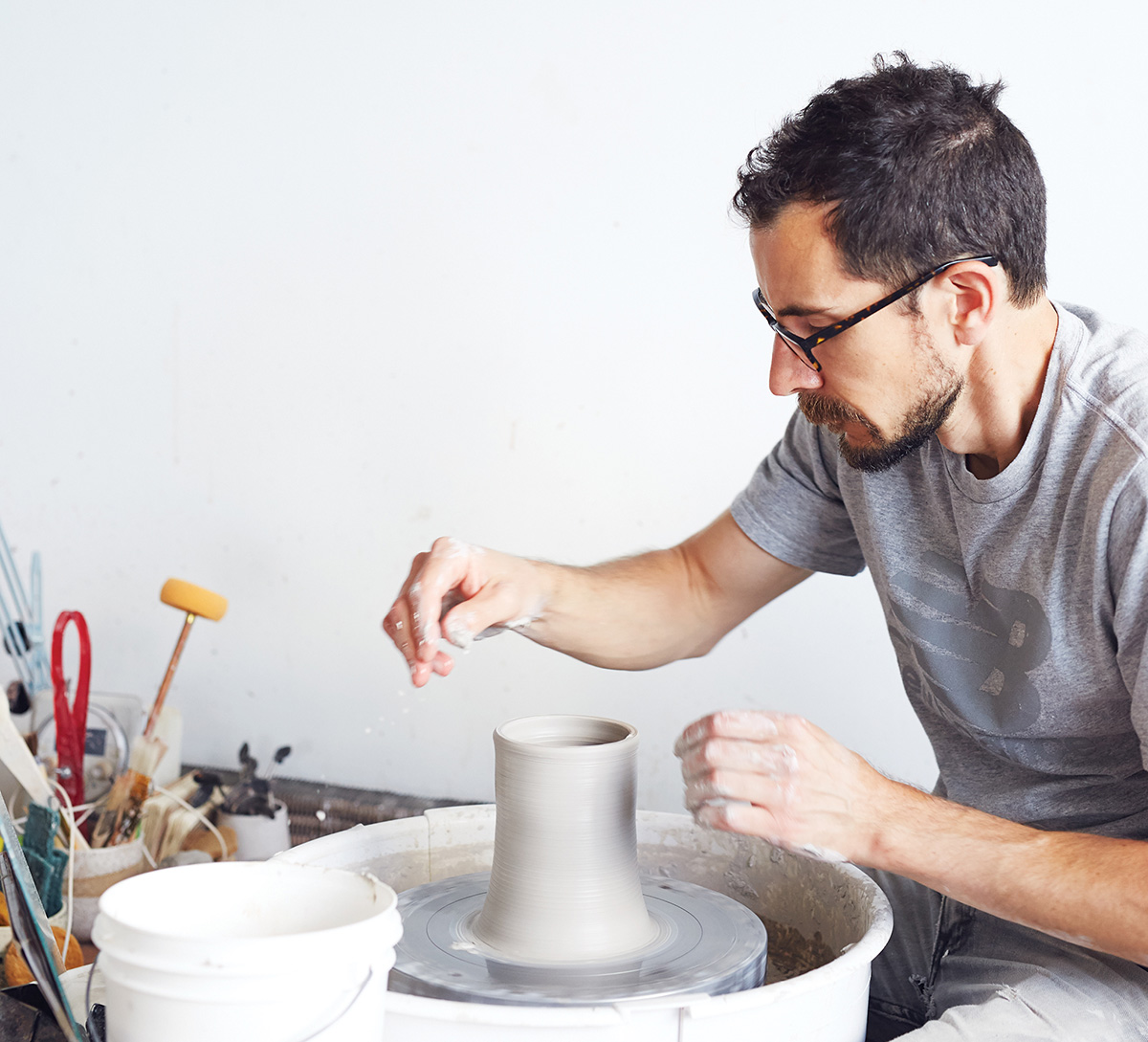
Eric throws a vessel on the wheel. / Photograph by Pat Piasecki
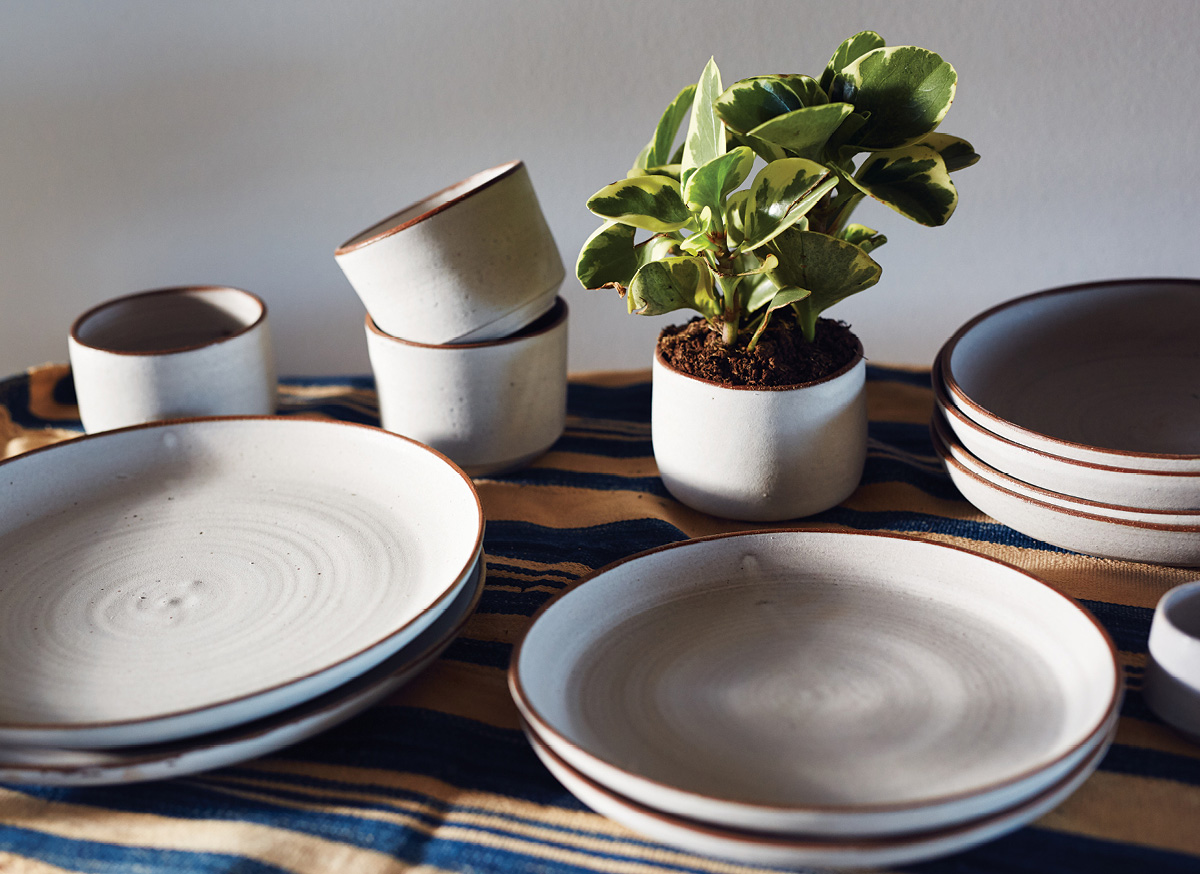
Myrth Ceramics’ product line includes stoneware plates and bowls. / Photograph by Pat Piasecki
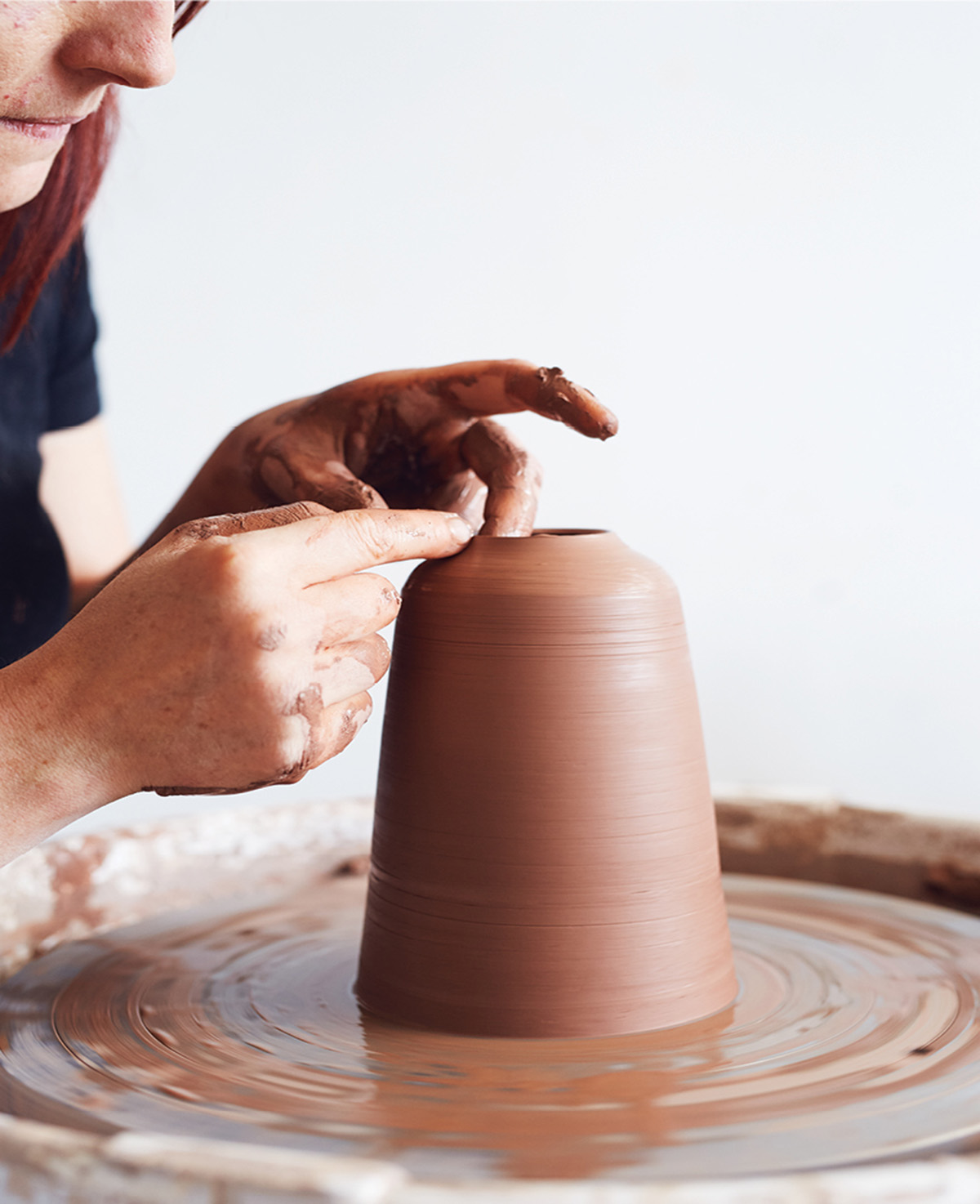
Abby says she uses water during the throwing process to help “move the clay upward while reducing drag.” / Photograph by Pat Piasecki
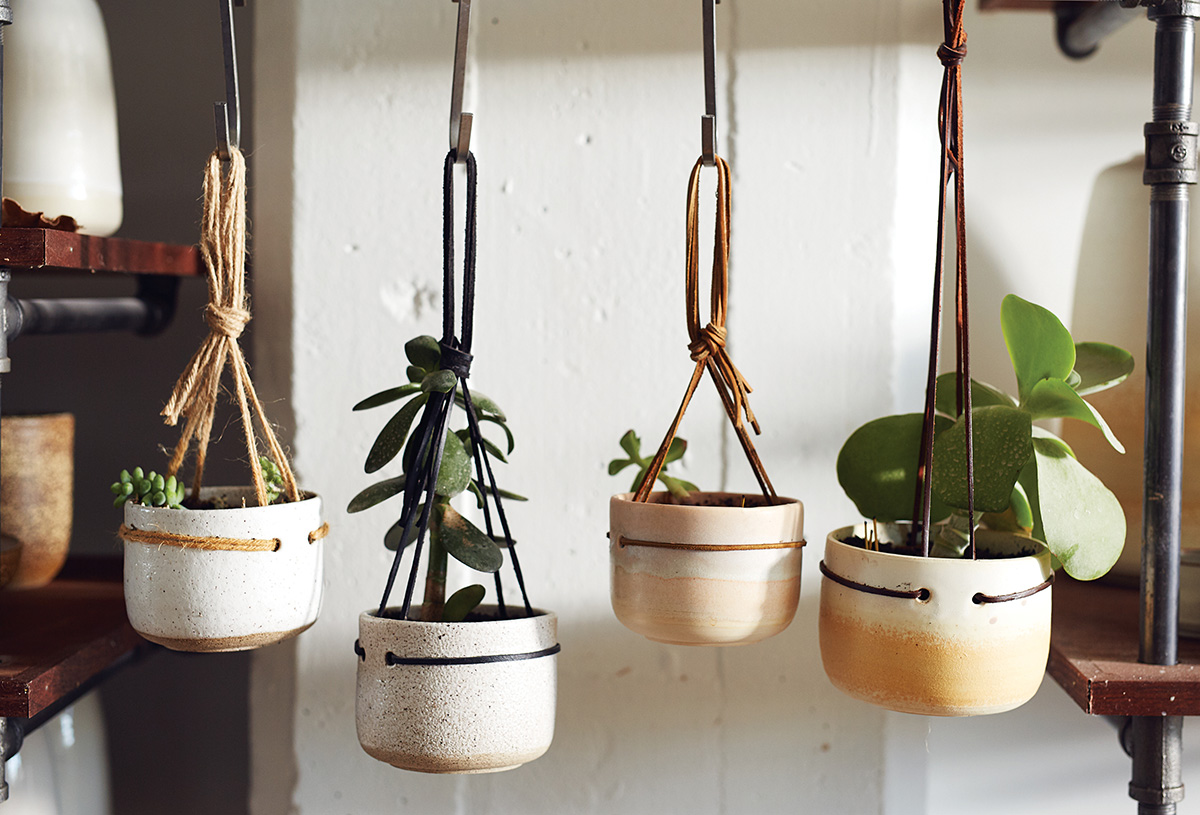
Accented with leather or vegan-hemp cord, these hanging planters are among the company’s most popular items. / Photograph by Pat Piasecki
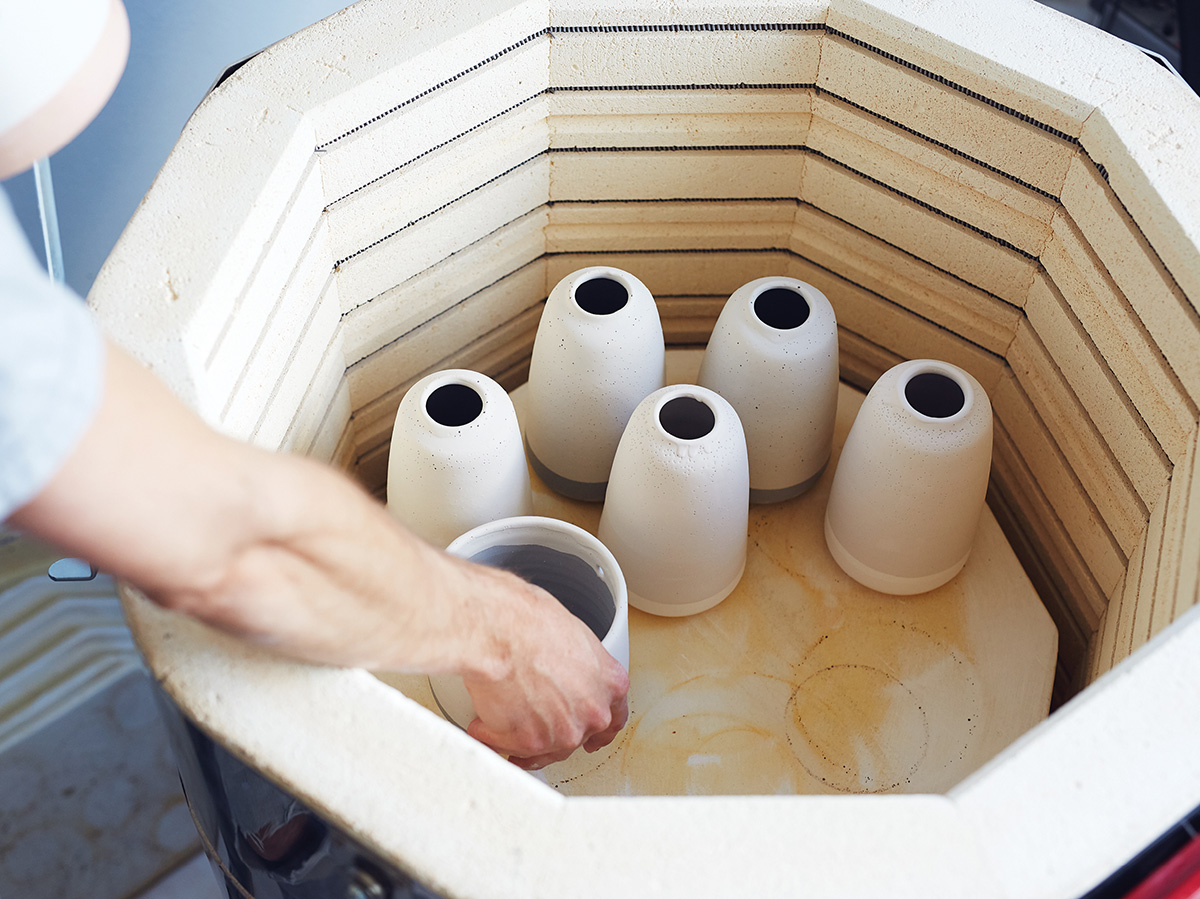
After the second and final firing, pieces must cool for 36 hours before they can be removed from the electric kiln. / Photograph by Pat Piasecki