This Woodworking Company Aims to Make Heirloom Pieces
Boston’s Cannon Hill Woodworking constructs striking, fully bespoke dining tables and more.
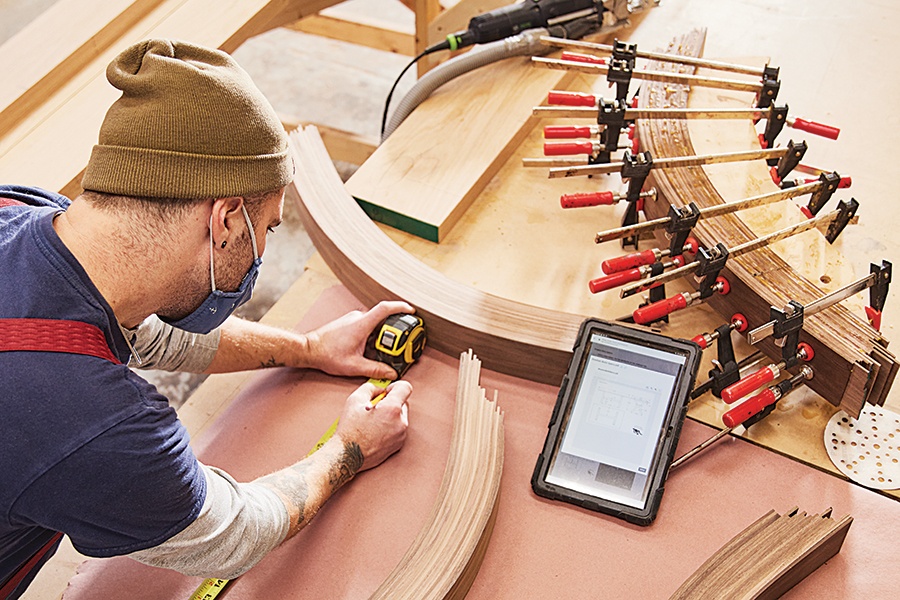
Making a curved table base requires stacking multiple slats of wood on top of one another—and plenty of planning. / Photo by Pat Piasecki
If Sam O’Leary could have one wish, it would be that his tables outlive him. “We’re trying to make heirloom pieces,” explains the cofounder and shop manager of Cannon Hill Woodworking, a Roxbury and Seaport–based custom woodworking company that specializes in dining tables. “When you deliver something and the client goes, ‘I’m going to give this to my kid [one day]’—that’s sick.”
Of course, it’s not as if a meal tastes better on a custom dining table than on a mass-produced one. (Or does it?) It’s more that mealtime becomes a little more meaningful when you throw bespoke work into the equation, O’Leary posits. “I think you appreciate your table more than if you picked something out of a catalog,” he says.
That ethos applies to more than just dining tables. Since starting the company in late 2018, cofounders Zack Hardoon and O’Leary, along with their first employee, Ross Ratner, have designed and fabricated all manner of wood creations for clients. They’ve produced bedroom sets, bookshelves, desks—which have seen a boom during the pandemic—dining hutches, and scores of coffee and side tables for local homeowners. They’ve even dabbled in the commercial space on a few occasions: notably, both Downeast Cider House and Castle Island Brewing Co. feature Cannon Hill tables in their Boston taprooms.
Putting high-quality, American-made woodwork into New England homes and businesses was always Cannon Hill’s goal, says Hardoon, who has a background in carpentry. “We’ve made a bet that if you give great customer service, help people understand every decision they make, and deliver a really slam-dunk product, that people will pay for quality,” he says. So far, it’s working out. Cannon Hill manufactured around 200 dining tables in 2021 alone, including one for a Hollywood A-lister’s Cohasset home. Also in the works is a seamless, patent-pending extension system for dining tables.
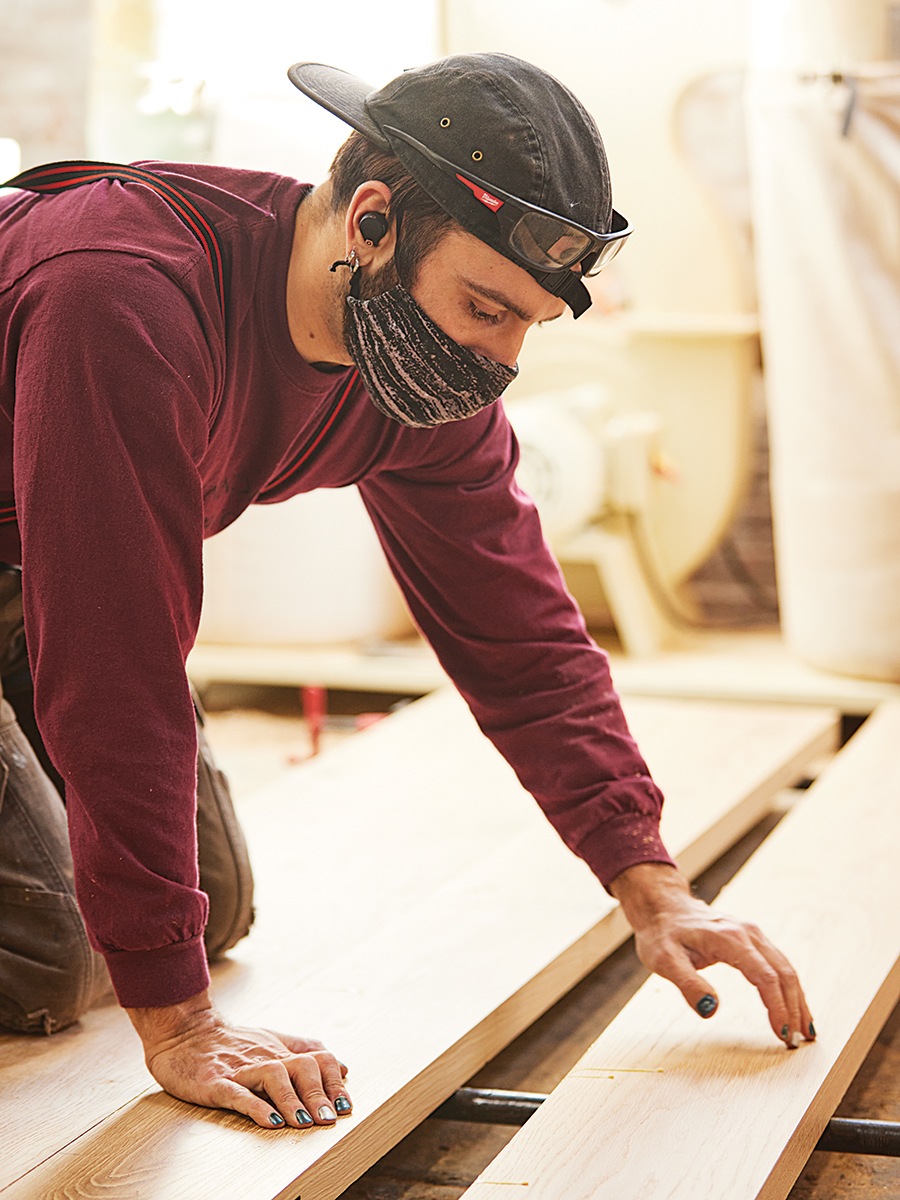
With little margin for error, the team’s work has to be “meticulous,” Zach Hardoon says. / Photo by Pat Piasecki
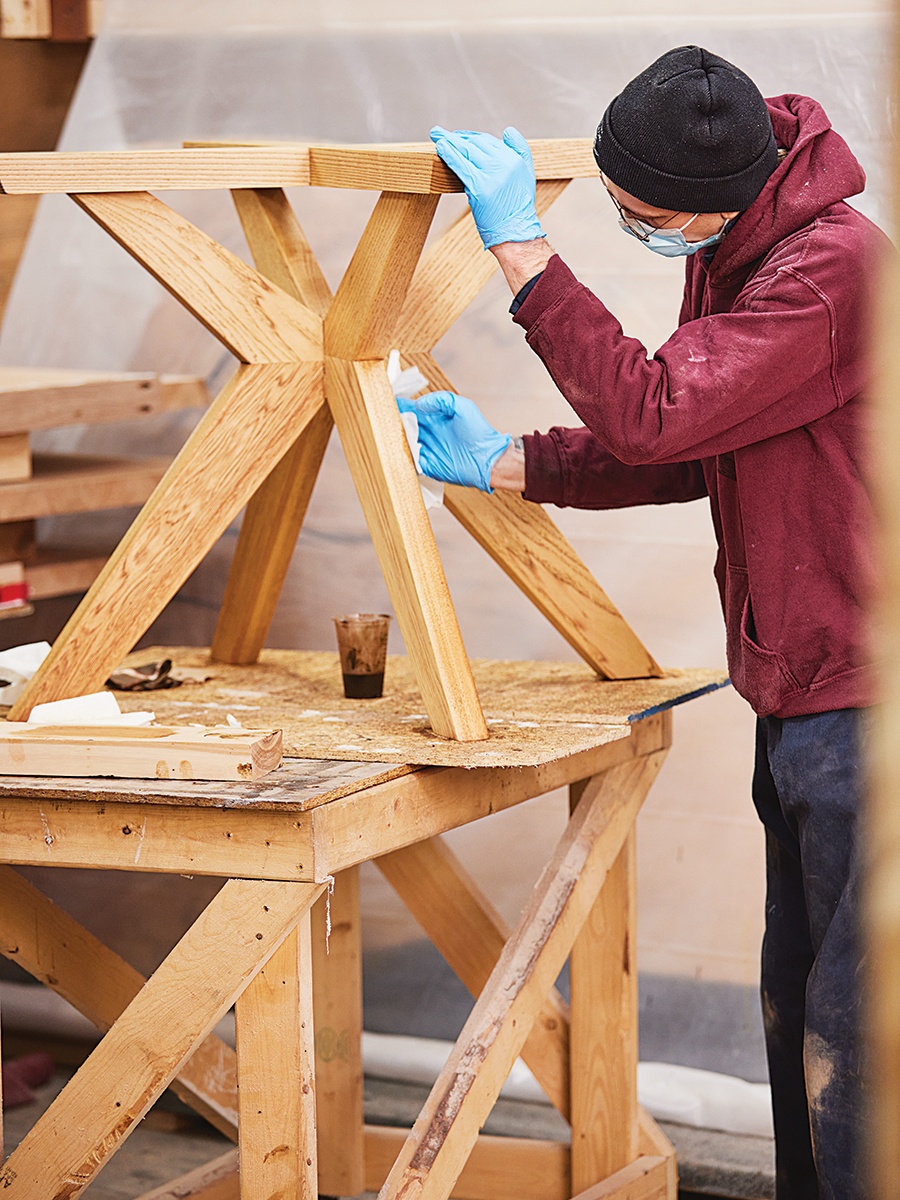
Although Cannon Hill specializes in dining tables, it also manufactures scores of smaller ones, like this round pedestal table. / Photo by Pat Piasecki
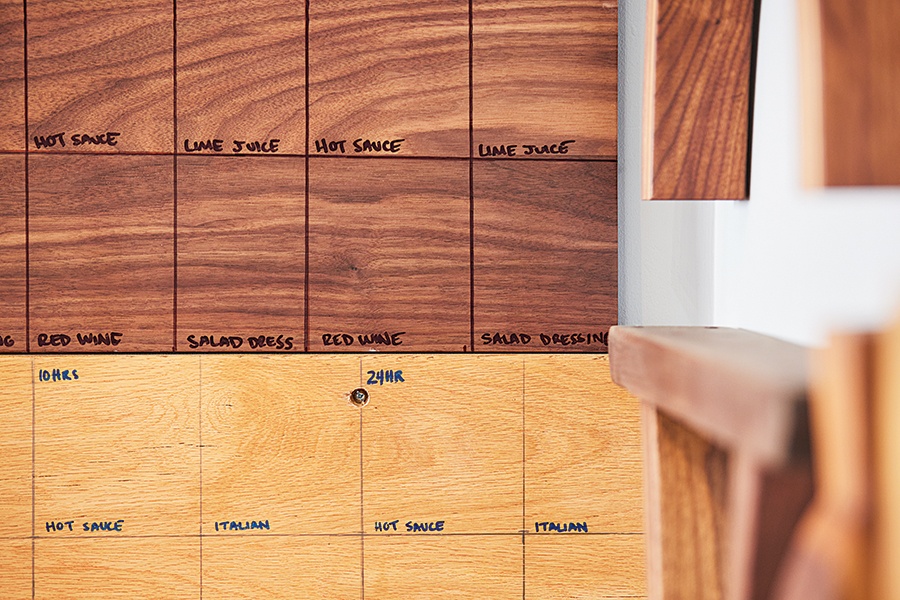
A sample board from the company’s Seaport showroom indicates the durability of different finishes. / Photo by Pat Piasecki
Dining tables make up about 90 percent of Cannon Hill’s business, O’Leary says. Most are made from white oak or black walnut, and sometimes reclaimed wood. Perusing the company’s Instagram reveals just how much range the furniture staple can hold: There are farmhouse-style, midcentury-modern, and contemporary tables, as well as plenty of live-edge pieces, as always.
And all are made-to-order. For a live-edge table, the client first picks out a hardwood slab from lumber company Berkshire Products’ inventory, either in-person or online. Once they settle on a slab, Berkshire ships it to Cannon Hill’s Roxbury workshop. One perk of working with Berkshire: Since the supplier’s slabs are almost always fully dried, the Cannon Hill team can get to work as soon as one arrives. (With other suppliers, the team sometimes has to store the slabs away to dry—a process that generally takes “a year for every inch thick” a slab is, O’Leary explains.)
Because wood naturally comes with imperfections—like splits and dead spots—the builders have to determine how to cut a slab down so clients
get the best-looking table possible. Once they have a roadmap figured out, they call the client for a sign-off: “We never cut without the customer’s approval,” O’Leary says. After cutting the slab with a track saw, a circular saw mounted on a metal track, it’s time to address the imperfections.
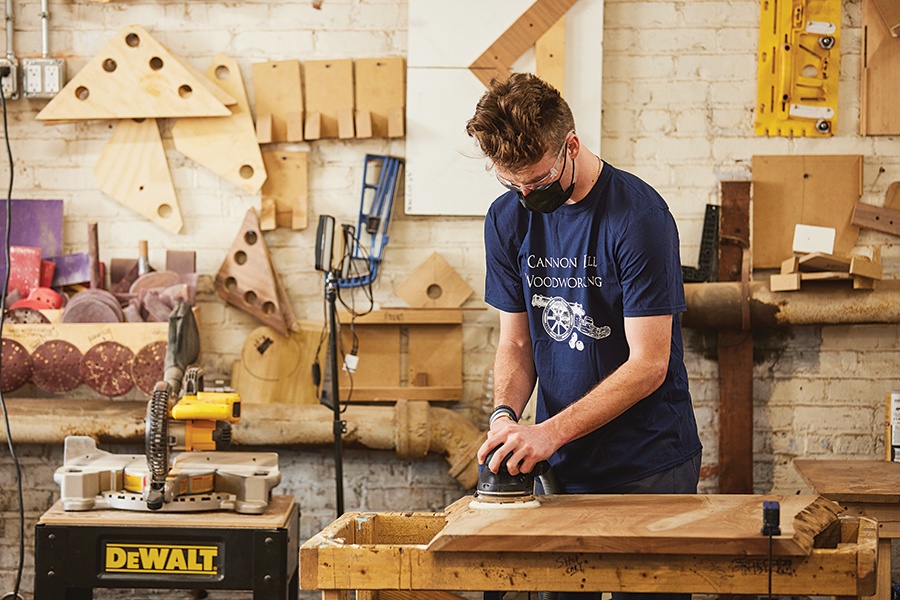
One of the final steps for making a tabletop is to sand it down until it’s perfectly flush. / Photo by Pat Piasecki
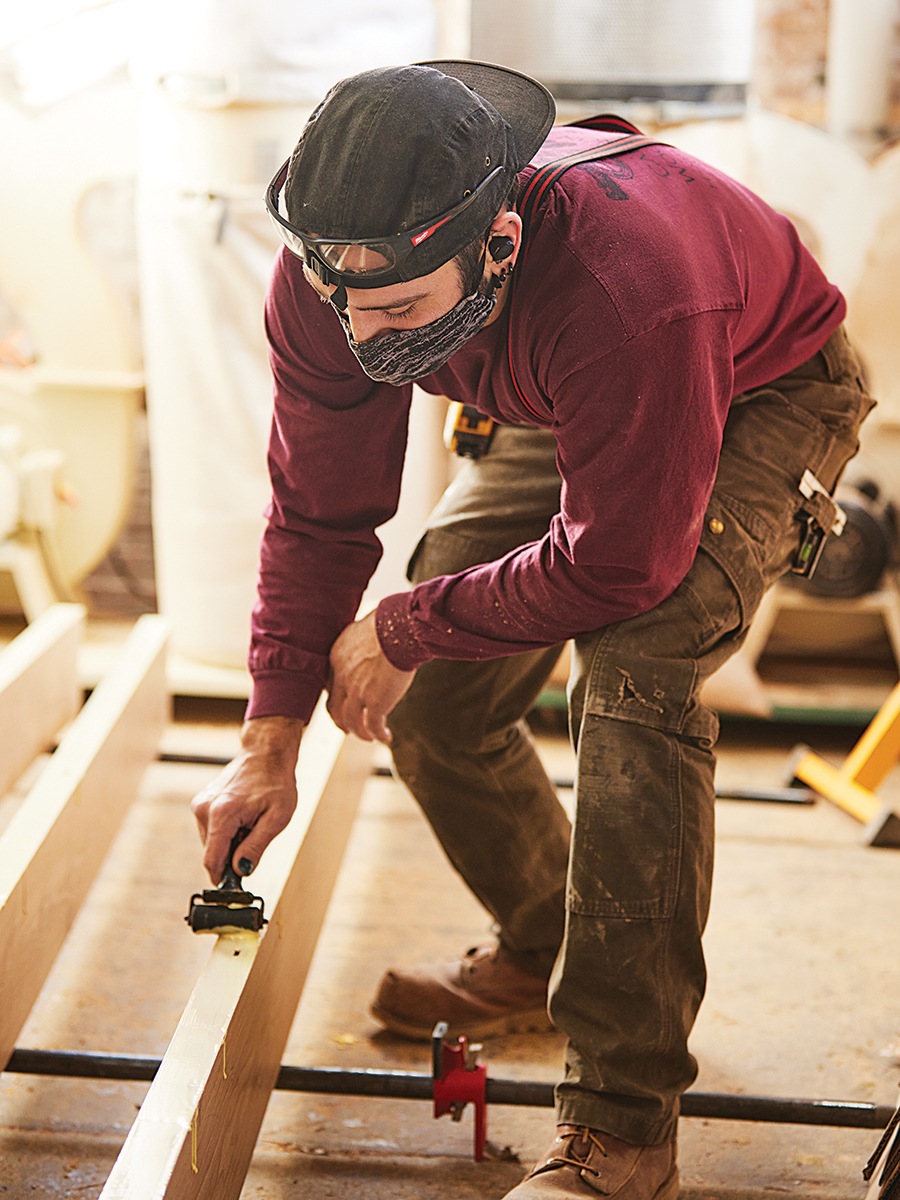
The pieces of a tabletop are glued together. / Photo by Pat Piasecki
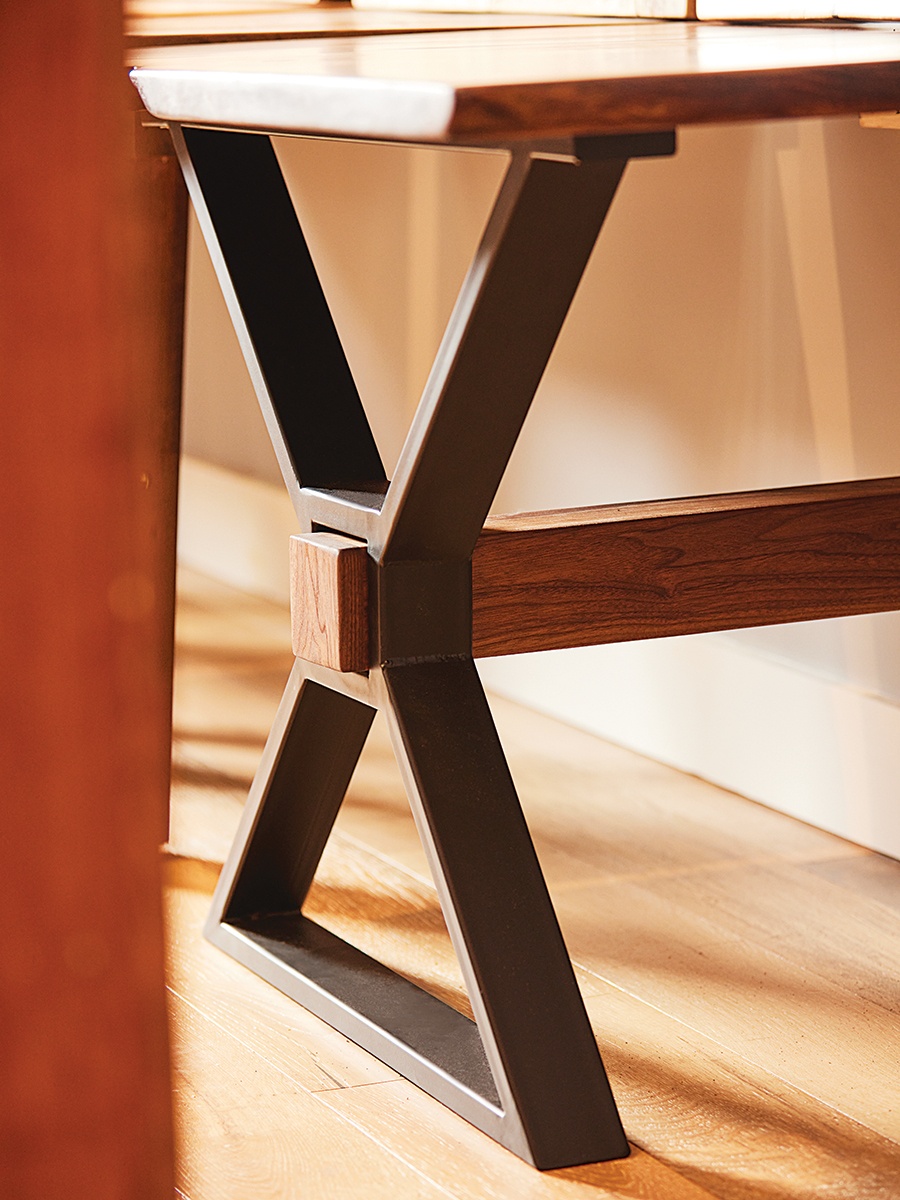
A trestle-style wood-and-metal base is a functional work of art. / Photo by Pat Piasecki
Any textural irregularities get shaved off with a hand planer (basically a cheese slicer for wood) until the slab is nice and flat. For a split—also known as a “check”—builders glue in “bow-ties,” or tapered wood inserts, to keep the split from spreading. For cracks, knotholes, or “voids,” they fill the offending spot with layers of epoxy, surrounded by a border of caulking to prevent seepage, and let it cure for a day or two.
Then come the finishing steps. Workers use sanders of varying grits to sand the slab until it’s level and smooth, finishing with a high-level polishing sander. To seal the tabletop, they apply either an oil or spray finish, retaining the natural color of the wood. The final touches are where Cannon Hill’s attention to detail really shows, Hardoon explains. “Once you put the finish on, you want everything that you did underneath it to be perfect, or else you have to work backward,” he says. “It’s very careful and meticulous work to get these things to our level of standards.”
Finally, it’s time to work on the base. To make one of Cannon Hill’s “X” pedestal bases, which feature a steel beam punching through a wooden slab, O’Leary draws up a design in a rendering program. He sends the design to a welder friend, who then welds the steel beam in his workshop. While he’s welding, Cannon Hill builders are making the wood part of the base: They cut boards (of the same wood as the tabletop) down to size, plane them and sand them, then cut notches in each side, gluing them together around the beam. Final assembly takes place during installation—workers slide the steel and wood into place, screw them into the tabletop, and voilà! A happy customer has a brand-new, completely custom dining table.
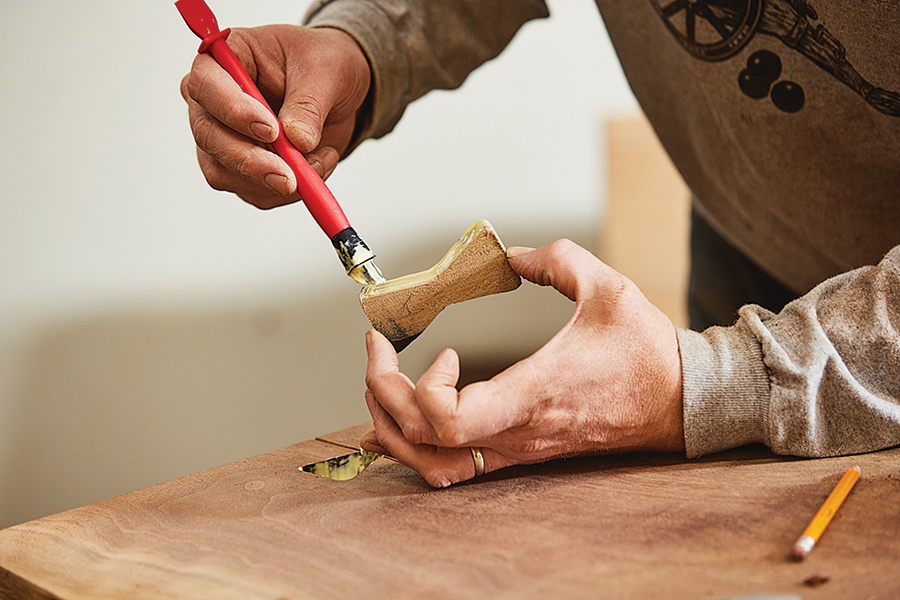
Builders use “bow-ties,” or tapered wood inserts, to keep splits from spreading. / Photo by Pat Piasecki
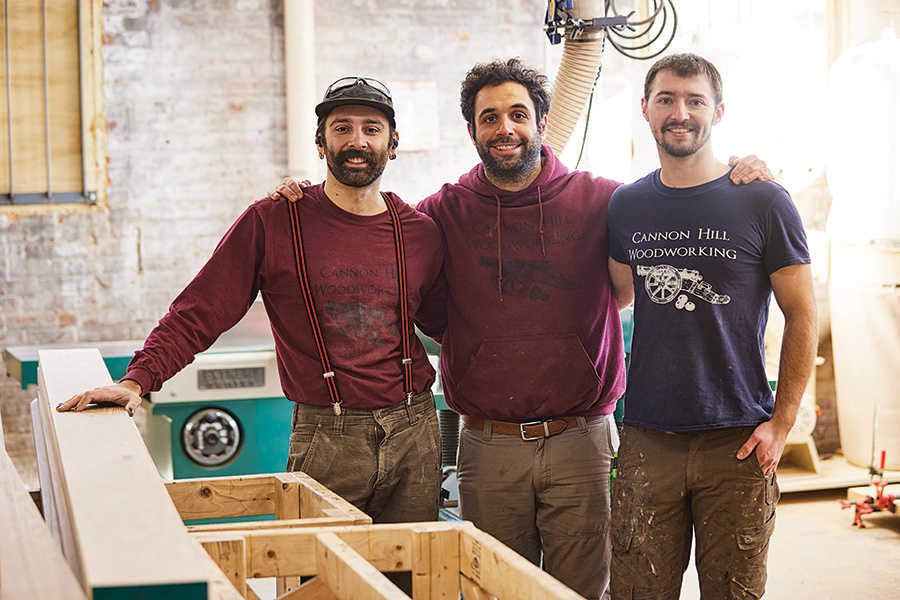
From left, Cannon Hill’s first employee, Ross Ratner, and cofounders Zach Hardoon and Sam O’Leary, who started the company in 2018. / Photo by Pat Piasecki
Recently, Cannon Hill has seen an uptick in repeat customers. That alone makes the team’s hustle worth it, says Hardoon, recalling the earliest days when it was just him and O’Leary making one table a week. “There were times when we’d both just like, burst into tears from stress,” he admits.
Now, Cannon Hill is up to nine staffers who put out around four tables a week on average. Hardoon and O’Leary have toyed with the idea of adding a third space to the Cannon Hill family just for processing live-edge slabs, in addition to the Roxbury workshop and Seaport showroom. But until that
happens, they’re staying committed to the original goal: making kick-ass products for folks who appreciate design and craftsmanship.
“I don’t ever want to buy cheaper materials or cut corners,” Hardoon says. “We’re going to stay devoted to creating a perfect product and process, and making the nicest, most-custom tables that you can find.”