Natural Selection
Using raw materials, Merida weaves time-honored skills with modern techniques to create its art-inspired, sustainable rugs out of a Fall River factory.
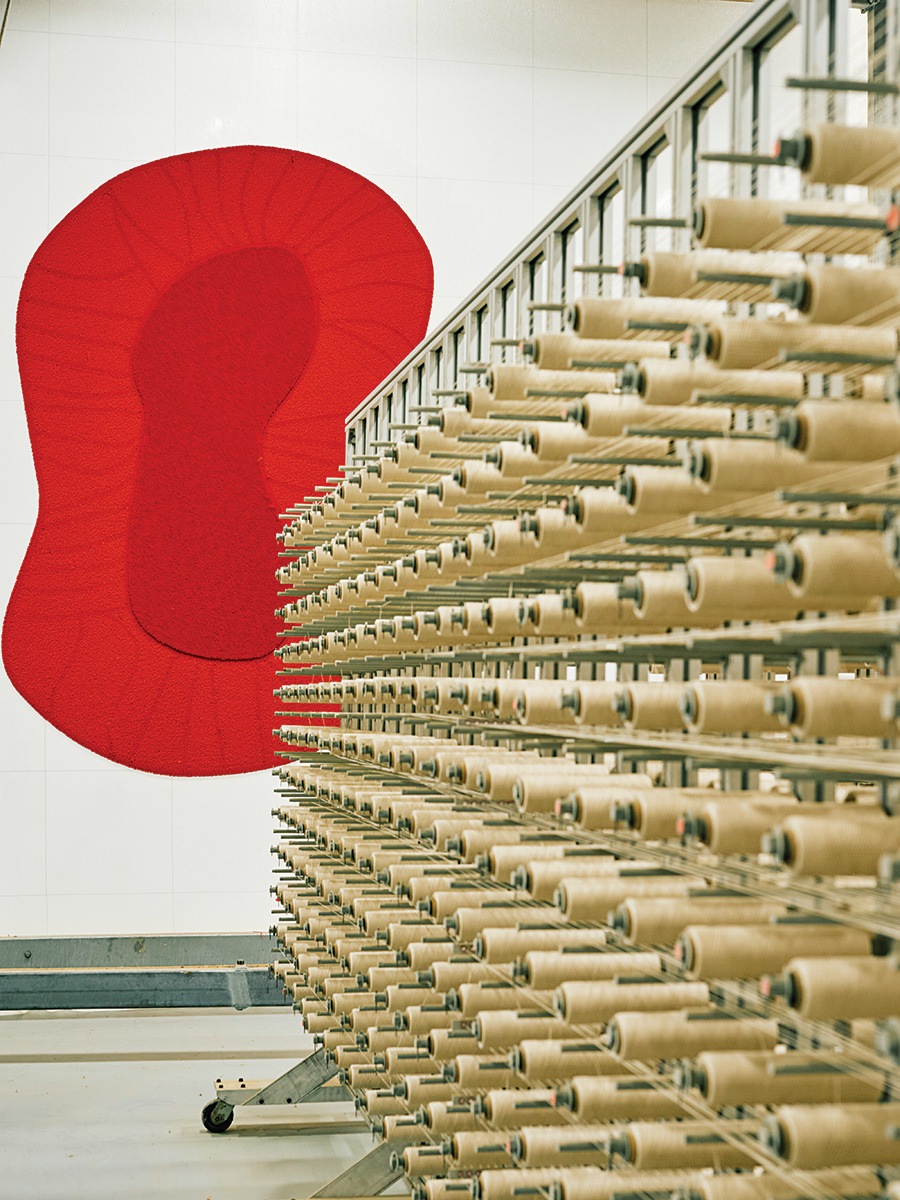
On display, “Reef” in Lava is a new release that features multi-felted merino, linen, and crimped, thin-felted, and silk wools. / Photo by Kelly Davidson
Launched in the late 1970s in Syracuse, New York, the story of Merida and its products spins an interesting tale. Originally importing sisal as wallcoverings for the Church of Jesus Christ Latter-Day Saints, the company ended up being the first to figure out how to cut it, bind it, and use it for rugs. “Throughout the ’80s and ’90s, Merida had a monopoly on finished sisal and sold through carpet dealers and showrooms,” Catherine Connolly, owner and CEO, says. “When I came in 2007, we realized that the knockoff sisal from China was starting to take hold. The company has always cared about natural materials and its employees, so I said we need to start manufacturing wool products from scratch here instead of importing sisal and finishing it.”
That’s when the team started thinking about manufacturing in Fall River, Massachusetts—a small city that was considered the Silicon Valley for textiles back in the 1850s—and whether or not they could commit to using all-natural products. “We realized that in order to move in this trajectory, we needed to sell directly to designers instead of through wholesale, so we did it.” Then about seven years ago, Connolly realized that the only way Merida could survive in Massachusetts was to do something extraordinary. That led to hiring Sylvie Johnson, a brilliant weaver based in Paris, as the company’s artistic director to work with the team and make Merida’s own yarns, begin blending, and learning new techniques to elevate the craft—all while simultaneously investing in the time it takes to do it successfully. “Now, as opposed to being a manufacturer, we’re more of an artisan workshop making these one-of-a-kind rugs in Fall River,” Connolly says.
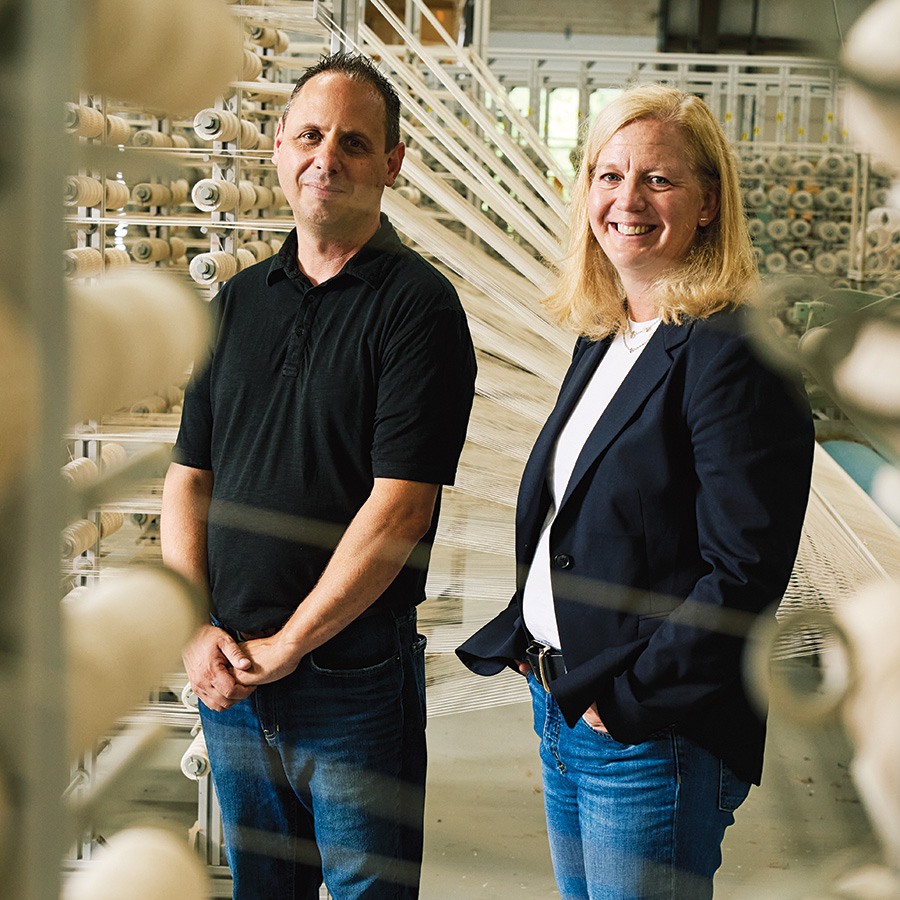
Manny Sousa and Catherine Connolly. “One of the most wonderful aspects of Merida is that we’re in Fall River, and there’s so much generational talent,” Catherine Connolly says. “For example, some of our weavers learned the craft when they were 16 years old. Now they’re passing down their skills to some of our younger weavers who are coming in.” In fact, the company has a few father-and-son employees. “It’s amazing to see both the skill that’s being passed down and how we’re building on that skill and adding to it,” she adds. / Photo by Kelly Davidson
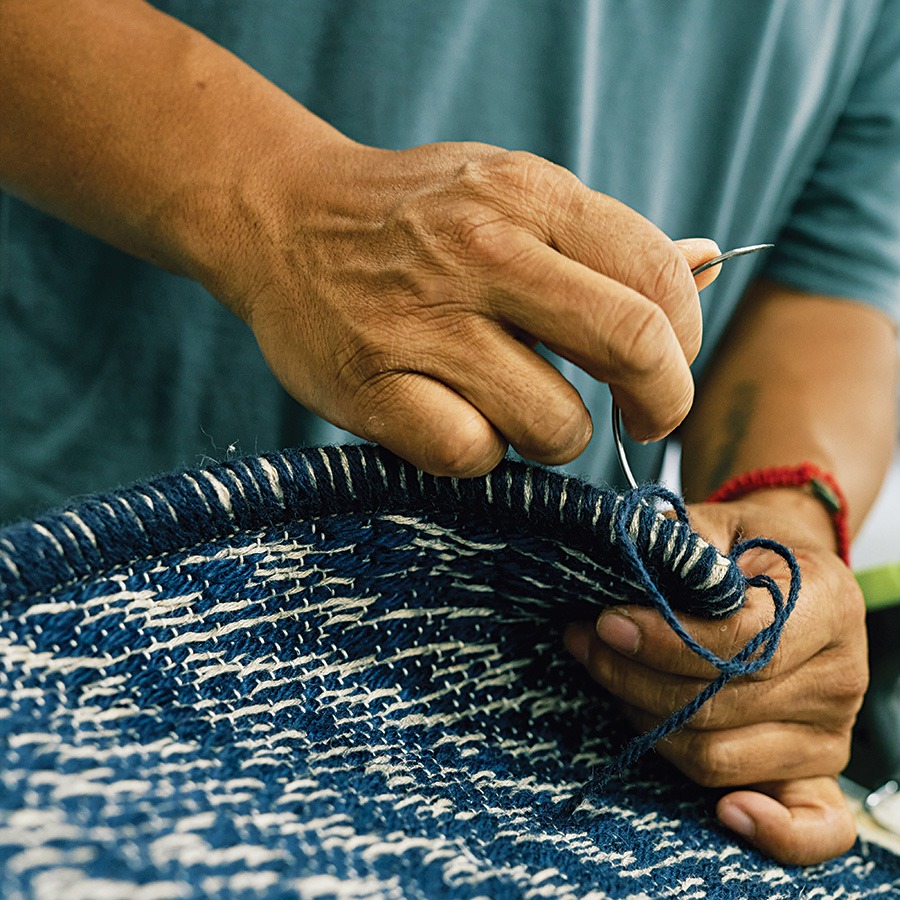
Connolly continues, “What I know about the craftsmen is that you can see them thinking with their hands. Weaving is very mathematical. They all have great mathematical minds, and their hands are thinking literally as their brains are—it’s just an amazing process to see because it’s a little bit of sixth sense. / Photo by Kelly Davidson
This process began with Connolly and Johnson sitting down and developing a five-year plan. “We started to think about how we introduce certain colors and new yarns,” Connolly explains. “For example, we used to use just three different types of yarns; now we use 11. With each collection, Sylvie works with our team to think through how to combine different yarns before we even start weaving or tufting to create different effects.” They also think about durability, beauty, and how light and shadows play off each other. Johnson is usually inspired by different art movements. This year’s collection was based on Arte Povera; next year will be Land Art. “Once Sylvie has the vision, colors, and yarn types, she starts working with our team of designers, and then all of our craftsmen work together,” Connolly notes. “They spend about a year working on different prototypes—taking an idea, turning a sketch into a CAD, and then thinking about the different yarns and colors.” The result? Each year, Merida comes out with 36 pieces in each collection.
Connolly notes that there are three main avenues of construction, in addition to some handweaving. “We work off a robo-tufter, which basically mimics handtufting. Then we have our jacquard looms, which have different types of yarns and employ different types of techniques, and then there are the dobby looms, which mimic handweaving.”
Production manager Manny Sousa describes the work as taking new machinery and adding old-school techniques. “Even though we have mechanical machines that do the weaving, we’re also doing a lot of handweaving in unison with that machine,” he notes. “We take the designer’s vision and make it happen here in our production area. We can take any yarn type, any color, and twist them together to make one singular yarn—it’s almost like mixing paint.”
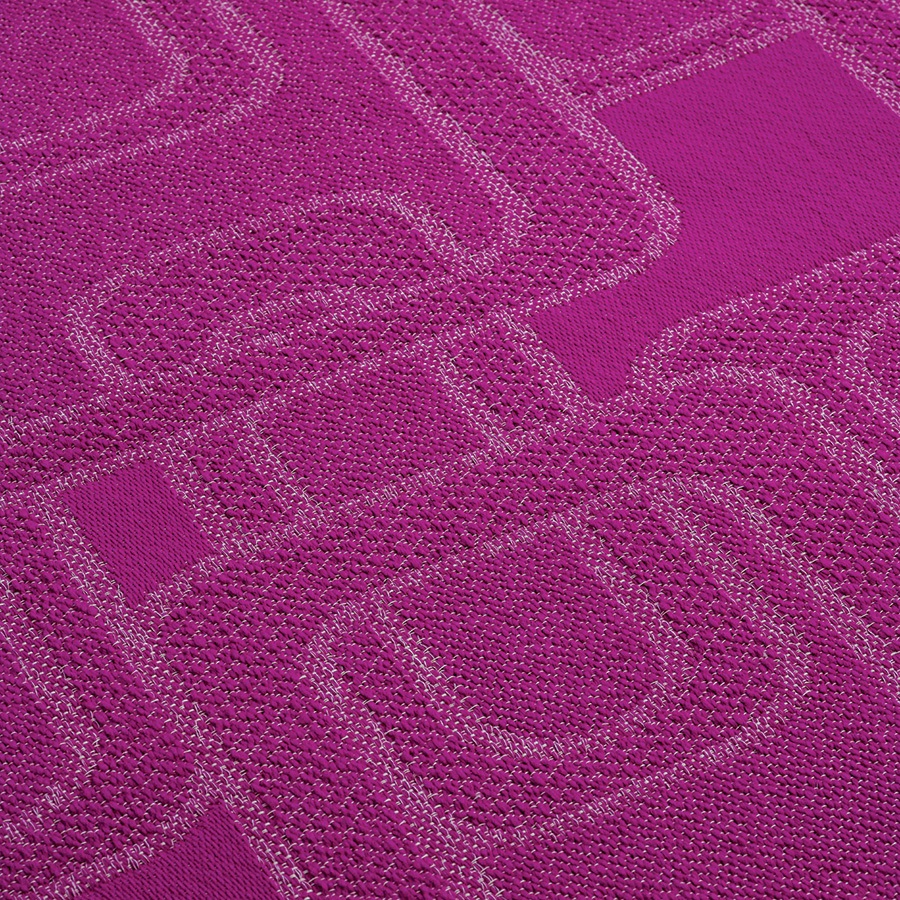
From the Atelier Collection, “Gamen” is a modern statement of texture and color with a graphic motif inspired by the pipe sculptures of American artist Donald Judd. The materials used are all natural fibers, including wool, silk wool, mohair, and alpaca. There’s no use of any plastics. “We have what we call a GPA, which is the Green Products Assurance program. We’re certified by this third-party lab stating we do not use any hazardous chemicals,” Sousa says. “I used to talk about sustainability all the time because I was so excited about it…A lot of people felt like either I was using it for marketing or lecturing, so then I decided we’re just going to make beautiful products of all-natural materials,” Connolly concludes. “That’s enabled us to hire really talented designers and weavers because it’s a wonderful environment to work in.” / Courtesy photo
First published in the print edition of Boston Home’s Fall 2023 issue, with the headline, “Natural Selection.”